Przeglądając grawery laserowe na aliexpress, mistrz natknął się na kilka modeli zasilanych przez USB. Zaskakujące było to, że mogli grawerować na różnych materiałach, a także wycinać kształty i wzory z naklejek i papieru oraz wykonywać całą tę moc z 5 V USB. Wadą tych grawerów było to, że mieli niewielki obszar roboczy, w większości przypadków tylko 40 mm x 40 mm.
Następnie mistrz postanowił samodzielnie zaprojektować i wyprodukować grawer przy użyciu drukarki 3D do produkcji. Po drodze postanowił zrobić modułowy uchwyt lasera, aby laser mógł być łatwo zastąpiony długopisem lub markerem. Dodano również funkcję połączenia Bluetooth.
Dane techniczne grawera są następujące:
- Obszar roboczy 200 x 162 mm
Moduł laserowy -1000 MW
-Praca ze źródła zasilania USB (5 V)
-Automatyczna funkcja prowadzenia
- Komunikacja Bluetooth między grawerem laserowym a komputerem
- Sterowanie laserem PWM. (Pomaga w tworzeniu różnych odcieni czerni podczas grawerowania portretów)
Rozdzielczość -102,4 kroków na mm
- Maszyna może grawerować, ciąć i rysować na różnych materiałach
Narzędzia i materiały:
-Arduino UNO;
-Płyta rozszerzeń;
- sterownik silnika krokowego A4988 - 2 szt .;
Moduł laserowy -1000 mW;
- Arduino Nano;
- Konwerter doładowania XL6009;
- Liniowe łożyska kulkowe LM8UU - 6 szt;
Koło pasowe - 4 szt;
- Pręty o średnicy 8 mm, długość 300 mm -4 szt .;
-moduł IRF520 Mosfet;
- przekaźnik;
- Wyłączniki krańcowe - 2 szt;
-Step silniki 2 szt;
- Magnesy neodymowe 18 x 5 mm x 3 mm;
-30 * 30 mm 5 wolt wentylatora chłodzącego;
-Belt;
-HC-05 moduł Bluetooth;
-SG90 siłownik;
Zaciski śrubowe
-Shrink tube;
- Superglue;
Opaski kablowe;
- Łączniki
M3 30mm
Śruby M3 12 mm
M4 40mm
Nakrętki M3
Orzechy M4;
- Sklejka 8 mm 48 x 42 cm;
-5 mm przezroczysty arkusz akrylowy 22 x 22 cm;
- kabel MicroUSB;
-Zużyty papier;
-Nadfil;
- śrubokręt;
- Akcesoria do lutowania;
- szczypce;
- nożyczki;
-Szczypce;
-Komputer z oprogramowaniem;
Krok pierwszy: Projektowanie
Kreator rozpoczął od zaprojektowania podstawy i uchwytów wału osi Y. Ponieważ uchwyty składają się z dwóch identycznych elementów, funkcja lustra w Fusion 360 ułatwiła pracę. Funkcja lustra była kilkakrotnie wykorzystywana przy opracowywaniu tego grawera laserowego.W przeciwieństwie do innych programów CAD, jedną z doskonałych funkcji Fusion 360 jest to, że umożliwia tworzenie wielu komponentów na jednym ekranie z łączem do innych komponentów, tj. model może być zaprojektowany zmontowany.
Wysokość prowadnic osi X zależy od ogniskowej zastosowanego lasera. Musisz tylko upewnić się, że wysokość lasera mieści się w tym zakresie. Ostateczne ogniskowanie wiązki lasera można wykonać poprzez regulację soczewki lasera.
Fusion 360 pozwala również wybrać wygląd i materiał komponentów, aby ostateczny wygląd wyglądał naprawdę. Program pozwala konwertować i zapisywać opracowane komponenty bezpośrednio w formacie STL do drukowania 3D.
Poniżej możesz pobrać plik Fusion 360 z projektem grawera.
grawer laserowy v16.f3d
Krok drugi: Drukowanie 3D
Następnie kreator zaczyna drukować szczegóły. Wszystkie części są zaprojektowane w taki sposób, że można je łatwo wydrukować na drukarce 3D bez podpór.
Kreator drukuje szczegóły na drukarce TEVO 3D.
Materiał: PLA (Dark Green)
Wysokość warstwy: 0,3 mm
Wypełnienie: 30%
Grubość ścianki: 0,8 mm
Grubość góra / dół: 0,9 mm
Pliki do wydrukowania można pobrać klikając na to link.
Krok trzeci: Montaż osi Y.
Kreator zaleca otwarcie pliku kompilacji Fusion 360 na PC przed złożeniem. Pomaga to uczynić proces kompilacji bardziej zrozumiałym.
Kreator instaluje pręty i łożyska liniowe. Mistrz zaprojektowany tak, aby uniknąć klejenia części, tj. dopasowanie jest ciasne. Pręty muszą być wypełnione w gnieździe młotkiem.
Po montażu upewnij się, że karetka porusza się swobodnie.
Krok czwarty: komputer stacjonarny
Na akrylowym arkuszu wierci się otwór. Przykręca arkusz do karetki i ustawia krawędzie arkusza dokładnie równolegle do krawędzi karetki. Zaznacza i wierci cztery otwory montażowe. Wkręca akryl do wózka.
Krok piąty: oś X.
Następnie mistrz zbiera oś X. Prowadnice dla osi zostały wydrukowane przez mistrza, ponieważ te, które kupił, okazały się wadliwe. Według niego, po szlifowaniu i nasmarowaniu przewodniki te działają nie gorzej niż zakupione.
Krok szósty: przerobienie silnika jednobiegunowego 28BYJ-48 na bipolarny
Istnieją dwa główne powody, dla których należy przekształcić silnik jednobiegunowy w silnik dwubiegunowy.
Algorytm sterowania silnika bipolarnego wykorzystujący sterownik silnika krokowego A4988 jest prostszy niż sterowanie silnikiem jednobiegunowym
Karta rozszerzeń obsługuje tylko bipolarne silniki krokowe.
Możesz przerobić silnik w trzech krokach.
Otwórz niebieską plastikową obudowę, odłącz czerwony przewód od płyty, jak pokazano na pierwszym zdjęciu.
Teraz musisz uszkodzić ścieżkę, jak na drugim zdjęciu i zmienić przewody w bloku, jak na trzecim zdjęciu.
Siódmy krok: instalacja silnika, koła pasowego, paska
Instaluje silnik. Na wale silnik zabezpiecza koło pasowe. Drugie koło pasowe ustawia się po przeciwnej stronie silnika. Zapina koniec paska za pomocą opasek. Przekazuje drugi koniec paska przez koła pasowe, a także mocuje.
Krok ósmy: Fundacja
Podstawa wykonana jest ze sklejki. Do niego mistrz przyczepia oś X.
Krok dziewiąty: oś Y.
Zbiera oś Y. Jest to trudny krok.
Zamontuj uchwyt koła pasowego za pomocą uchwytu koła pasowego osi Y, koła pasowego, śruby / nakrętki M4 40 mm i metalowych podkładek, jak pokazano na dwóch pierwszych zdjęciach.
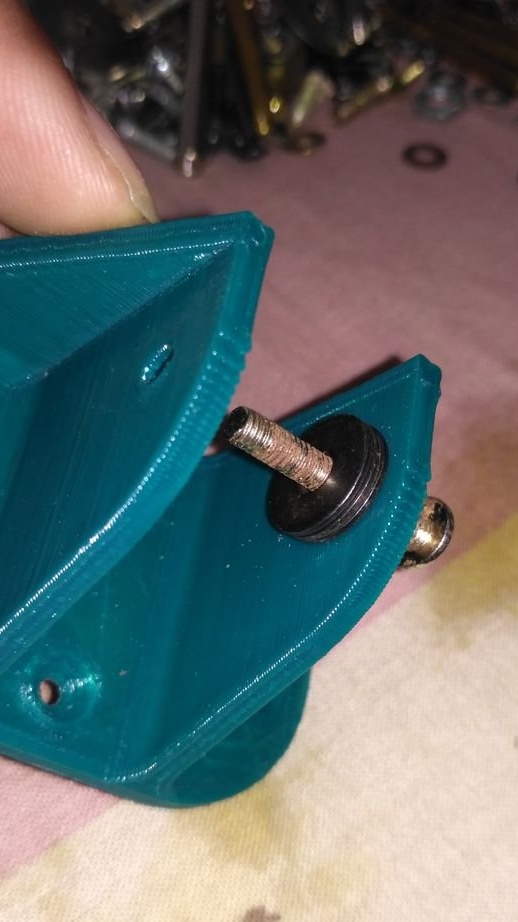
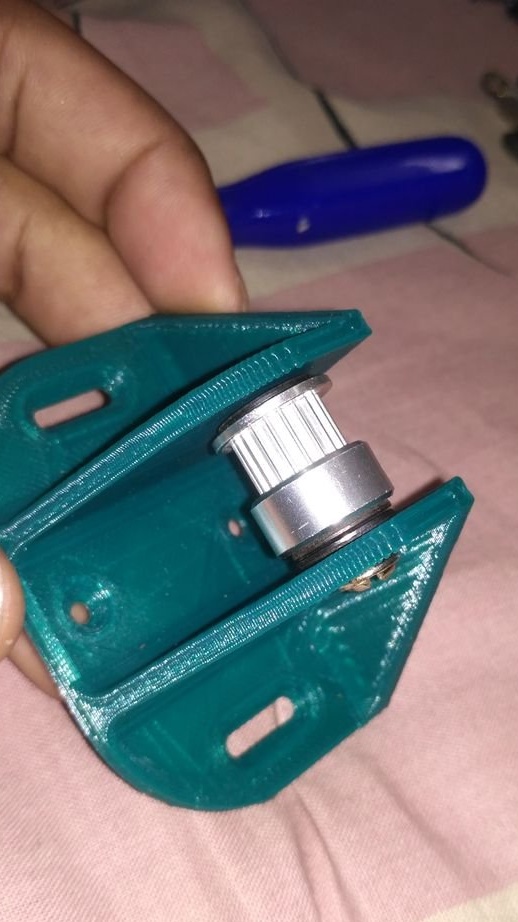
Teraz przywiąż jeden koniec paska rozrządu do jednego ze szczelin pod suportem osi Y.
Przełóż wolny koniec paska przez zespół koła pasowego, który wykonałeś wcześniej, a następnie zatrzaśnij go w drugim rowku znajdującym się pod suportem osi Y.
Po wykonaniu tych 3 kroków należy przykręcić zespół osi Y do podstawy sklejki.
Przymocuj silnik krokowy do mocowania silnika w osi Y za pomocą dwóch śrub M3 i nakrętek 12 mm.
Teraz przykręć uchwyt koła pasowego osi Y i wspornik silnika do podstawy ze sklejki.Zrób to po wyregulowaniu obu stron, aby uzyskać prawidłowe napięcie paska. Napinacz paska zostanie dodany później.
Krok dziesiąty: moduł laserowy
Jak wskazano, w specyfikacjach maszyna wdrożyła szybką wymianę modułu laserowego na inne moduły wykonawcze. W tym celu mistrz wykonał dwie prostokątne części (pokrywy). W każdym zainstalowano sześć magnesów neodymowych. Jedna pokrywa jest przymocowana do osi X, moduł laserowy jest przymocowany do drugiej.
Przewody są montowane w następujący sposób.
+ i - lasery są podłączone odpowiednio do V + i V- modułu MOSFET. Zasilanie jest podłączone odpowiednio do VCC i GND. Przewód sygnałowy jest podłączony do styku sygnałowego modułu MOSFET.
Krok jedenasty: Ploter
Zbiera ploter. Gdy tylko obie części zostaną wydrukowane, master poleruje płaszczyzny, które stykają się ze sobą, wygładza je pilnikiem i papierem ściernym, aż obie części ześlizgną się z bardzo małym tarciem.
Teraz dokręca śruby M3 40 mm i ustawia sprężynę.
Silnik serwo, zaciski i drążki Arduino, jak pokazano na zdjęciu.
Tutaj Arduino nano służy do konwersji sygnałów sterujących lasera na sygnały PWM, które mogą napędzać mikrosilnik.
Jest on połączony w następujący sposób:
+5 Volt - Vin
-5 V - GND
Sygnał - D10
Moc serwomechanizmu + ve - 5 V.
Servo power -ve - GND
Sygnał serwo - D3
Następnie kod jest ładowany.
#include Servo myservo;
void setup ()
{
myservo.attach (3);
pinMode [10, WEJŚCIE];
}
void loop ()
{
if (digitalRead (10) == HIGH)
{
myservo.write (20);
}
jeszcze
{
myservo.write (60);
}
}
Krok dwunasty: Instalacja
Instalacja zgodnie ze schematem.
Konwerter doładowania jest ustawiony na 12V.
Arduino jest zainstalowany w module rozszerzającym CNC.
Wentylator jest przyklejony do przewidzianego do tego otworu za pomocą kleju topliwego.
Dodano pasek LED zarówno dla wskazania wyglądu, jak i mocy.
Drukowana obudowa jest przykręcona do sklejki.
Przezroczysty arkusz akrylowy o grubości 87 x 75 mm 2 mm służy jako osłona korpusu. Można go wsunąć przez przewidziany dla niego rowek po jednej stronie obudowy.
Wyłączniki krańcowe są przymocowane w taki sposób, że przycisk zostaje wciśnięty 3 mm, zanim łożyska każdego wózka zderzą się z uchwytami trakcyjnymi.
Przewody silników i wyłączników krańcowych są wydłużone, a połączenia są izolowane.
Druty są przyklejone do podstawy ze sklejki za pomocą superglue.
Tutaj konwerter doładowania służy wyłącznie do zasilania układów sterownika silnika A4988. Każdy silnik zużywa tylko 150 mA prądu.
Krok trzynasty: moduł Bluetooth
Montuje moduł bluetooth.
Aby wysyłać i odbierać dane lub, w tym przypadku, kody G za pośrednictwem modułu Bluetooth HC05, należy najpierw skonfigurować moduł.
Podłącz moduł HC05 do Arduino Uno, jak pokazano na pierwszym rysunku.
Pobierz kod dołączony do tego kroku na Arduino.
BLUE_P.ino
Teraz wprowadź kody pokazane na drugim zdjęciu.
Po zakończeniu ustawień odłącz moduł HC05 od Arduino, którego użyłeś do programowania, i podłącz do Arduino CNC Shield zgodnie ze schematem połączeń na 3 zdjęciu.
Krok czternasty: kod i konfiguracja
W przypadku grawera laserowego mistrz pobiera kod.
GRBL.zip
Laser GRBL jest jednym z najlepszych darmowych streamerów kodów G dla grawerów laserowych. Może bezpośrednio przesyłać kody G do Arduino przez port som. Ma wbudowane narzędzie do konwersji obrazów na kody G.
Wszystkie ustawienia należy wykonać jak na zdjęciu, biorąc pod uwagę:
Zainstaluj port sumowy, do którego podłączony jest grawer laserowy.
Wartości konfiguracji można zmienić, aby najlepiej pasowały do grawera.
Krok piętnasty: Testowanie
Po podłączeniu lasera czas sprawdzić jego dokładność.
Jest kilka rzeczy do sprawdzenia:
Czy osie X i Y poruszają się we właściwym kierunku?
Czy bazowanie działa poprawnie?
Czy silnik omija kroki z powodu dużego tarcia lub zbyt ciasnych pasów?
Czy rozmiary drukowanych obrazów są zgodne z rozmiarami wskazanymi w oprogramowaniu. Czy liczba kroków na mm odpowiada zastosowanemu silnikowi krokowemu.
Naciąg paska można regulować za pomocą napinacza. Obracaj śrubę, aż do uzyskania prawidłowego napięcia.
Aby sprawdzić, czy silnik ma kroki i prawidłowe wymiary, wyślij prostą ciągłą figurę geometryczną, na przykład kwadrat, trójkąt lub okrąg. Jeśli laser zaczyna od jednego punktu i zatrzymuje się idealnie w tym samym punkcie, oznacza to, że laser nie przeoczył ani jednego kroku i działa idealnie. Po wydrukowaniu trójkąta lub kwadratu ręcznie zmierz jego rozmiar za pomocą linijki i sprawdź, czy pasuje do podanych wymiarów.
Według mistrza jest on całkowicie zadowolony z maszyny.
Można grawerować na różnych materiałach, takich jak drewno, karton, skóra, plastik itp.
Ponieważ silnik miał około 102 kroków na mm, można wykonać drobne ryciny z drobnymi szczegółami.
Grawer działał bez problemów na zasilaczu USB.