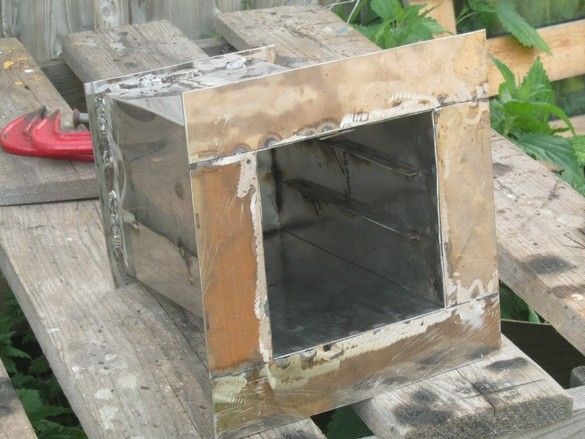
Specjalistyczne piece do wyżarzania szkła nieco różnią się od klasycznych pieców muflowych - temperatura wyżarzania, w zależności od rodzaju szkła, rzadko przekracza 600 ° C, co zmniejsza wymagania dotyczące materiałów do pieca, jednak w piecu do wyżarzania ważnym warunkiem jest jednorodność pola temperatur. Obie funkcje odpowiadają niecodziennemu wyglądowi. W rzeczywistości metal jest znacznie bardziej przewodzący ciepło niż materiały ceramiczne tradycyjne do pieców muflowych. Temperatura w metalowej obudowie jest znacznie bardziej jednolita.
W temperaturach poniżej 500 ° C stosuje się aluminiowe mufle, które przy odpowiedniej grubości ścianki (15 ... 20 mm) zapewniają szczególnie równomierny rozkład ciepła. Do 700 ° C stosowane są stalowe mufle, aw krytycznych przypadkach brązowe. Stalowe mufle najlepiej wytwarzać z żaroodpornych i żaroodpornych stali nierdzewnych pracujących w wysokiej temperaturze bez tworzenia się kamienia i odkształceń [1]. W przypadku małych mufli wygodnie jest używać segmentów metalowych rur.
Gdy szkło do wyżarzania, w którym bardzo ważna jest równomierność temperatury, mufle specjalnych pieców umieszcza się pionowo, tak jak na szalce [2], pozwala to uzyskać jednolite pole temperaturowe na przekroju pieca. Dalsze wyrównanie temperatury (grubościenna aluminiowa mufa (stal, brąz), układ pionowy) jest możliwe dzięki wymuszonemu mieszaniu powietrza w piecu i rotacji wyżarzonego produktu. Takie piece są stosowane do wyżarzania złożonych i krytycznych produktów.
Wytwarzanie metalowej mufy w kształcie kwadratu o pojemności około 5,5 l opisano poniżej. Mufla jest wykonana w warunkach dom warsztat, z blachy nierdzewnej o grubości 1,5 mm, metodą gięcia, łączenia - ręczne spawanie łukowe elektrodą topliwą.
Uzasadnienie wyboru materiału
Kilka blach stalowych pozostało bez oznakowania, jednak wykonano z nich pewną liczbę części do pieców opalanych drewnem, w tym tych regularnie narażonych na działanie silnego ciepła (wypalanie drzwi), praktyka wykazała, że nawet długotrwałe (lata) cykliczne narażenie na wysokie temperatury nie powoduje znacznych odkształceń strukturalnych. Tworzenie się skali jest również umiarkowane. Niskie odkształcenia były prawdopodobnie również wspierane przez skrzynkową konstrukcję zakończeń o stosunkowo małej powierzchni boków. Konstrukcja mufli jest podobna.Ponadto uzyskano pewne doświadczenie w stosowaniu tego materiału - techniki gięcia, dopasowania i spawania. Wszystko to ułatwi produkcję poczętego.
Muflowy design
Mufla jest cienkościenną (niestety) stalową skrzynką o kwadratowym przekroju, o boku 150 mm i długości 250 mm. Główna część mufy „rurowej” jest wykonana przez zgięcie, od prostego przeciągnięcia. Dno jest przyspawane do niego za pomocą małego kołnierza ~ 10 mm i dużego kołnierza (o szerokości 50 mm) na przedniej części, pokrywającego szczelinę na uzwojenie azbestowe (sznurkowe, kartonowe), które kompensuje rozszerzanie się mufy po podgrzaniu między muflą a solidną izolacją termiczną.
Aby rozszerzyć możliwości przyszłego piekarnika, na bocznych ściankach mufli znajdują się dwie pary szyn, równomiernie rozmieszczone na wysokości, podobnie jak piekarnik do pieczenia ciast. Umożliwi to zainstalowanie krat lub specjalnych uchwytów (na przykład dla szprych lampowych) i wyżarzanie znacznie więcej drobiazgów w jednym cyklu lub eksperymentowanie z równomiernym rozkładem temperatury poprzez zainstalowanie dwóch grubościennych metalowych płyt od góry i od dołu (po lewej od żeliwnej płyty kuchennej piec na drewno).
Nie ma otworu na termoparę - ma ona uszczelniać termoparę ze względu na wysoką przewodność cieplną ścian mufli pod grzejnikiem, izolując ją od metalu za pomocą płytki ceramicznej. Między innymi pozwoli to na bardziej swobodną pracę z wewnętrzną objętością przyszłego pieca, na przykład umożliwi konstrukcję zmieniającą położenie pieca - poziomo-pionowo.
Wygląd gotowej mufli widać w tytule.
Co zostało użyte do produkcji
Narzędzia
Zwykły zestaw narzędzi stołowych. Do cięcia blachy stalowej użyłem małej szlifierki kątowej z tarczą ścierną ø125 mm. Zdecydowanie zaleca się stosowanie słuchawek i okularów ochronnych. Narzędzie do znakowania - alkoholowy długopis lub metalowy „ołówek” - drapak z ostrym, utwardzonym nosem, duży kwadrat łączący, długa linijka. Do zamocowania części podczas cięcia spawalniczego użytecznych było kilka zacisków stolarskich. Do spawania wykorzystano mały falownik z akcesoriami - kable, maskę ochronną, skórzane getry, domowe ubijanie szklistego żużla z małego dłuta z rączką. Powinien także obejmować ciasne, niesyntetyczne ubrania i buty. Prace przeprowadzono na ulicy - przydał się dobry przedłużacz z parą (szlifierka kątowa, falownik) gniazd. Jak zawsze - absolutnie konieczna, odrobina cierpliwości i dokładności.
Materiały
Oprócz samej blachy stalowej potrzebne były elektrody spawalnicze - użyłem TsL-11, ø2mm i ściernych tarcz o średnicy 125mm, grubości 1 mm.
Do biznesu
Narysowałem skan na odpowiednim kawałku stali nierdzewnej. Przy grubości materiału 1,5 mm „naddatek” na zgięcia, pod warunkiem przycinania (co omówiono poniżej) - 1 ... 2 mm. Oznaczenie mianowania każdej ze stron nie zaszkodzi.
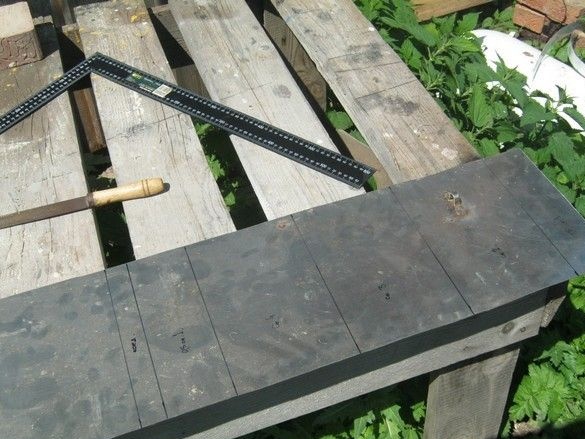
Przycinanie i cięcie zakrętu. Wszystko można łatwo zrobić za pomocą szlifierki kątowej w trzech przejściach - cięcie proste na połowie głębokości materiału i dwa cięcia na maszynie pod kątem 45 °. Szczegóły opisano w „zamknięciu drzwi”.
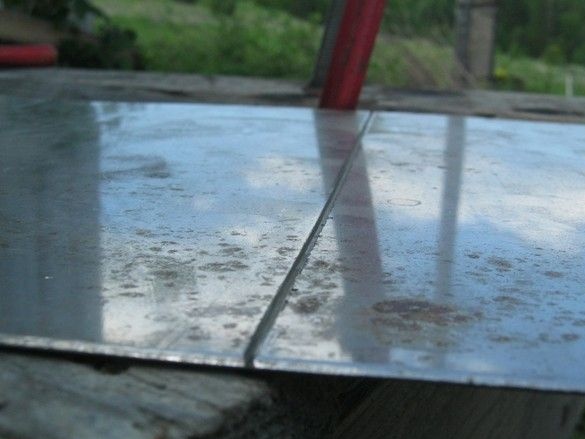
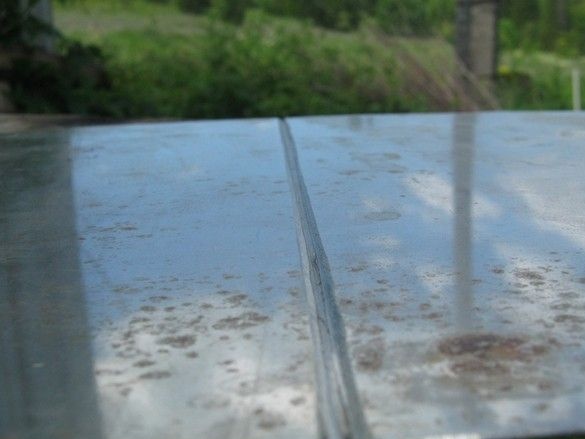
W ten sposób przetwarzamy każdy punkt zgięcia. Gięcie zostawiamy na słodko, w przeciwnym razie praca nie będzie wygodna. Połączenie końców skanu znajduje się na suficie kamery, pośrodku, więc wygodniej jest spawać. Zgrzewanie doczołowe cienkiej blachy za pomocą konwencjonalnego falownika, z moimi skromnymi umiejętnościami spawalniczymi - solidne wypalone otwory, dlatego umieść dodatkowy pasek pod szwem spawalniczym. Nie dopuściła do przegrzania krawędzi blachy stalowej, a stopione krople metalu płynęły do środka. Cieńsze półfabrykaty - prowadnice po bokach mufli. Widoczne oznaczenia do spawania. Długość prowadnic, nieco mniejsza niż długość mufli - nie powinny zaczynać się od samej krawędzi - pokrywa pieca z reguły ma „ćwierć” wokół obwodu, aby zmniejszyć straty ciepła. Wkłada go do mufli, blokując proste rozcięcie.
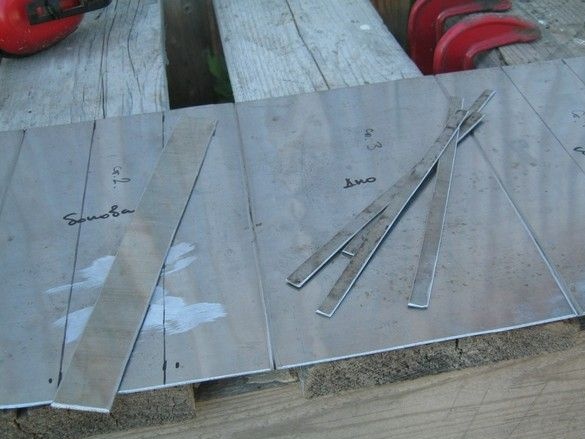
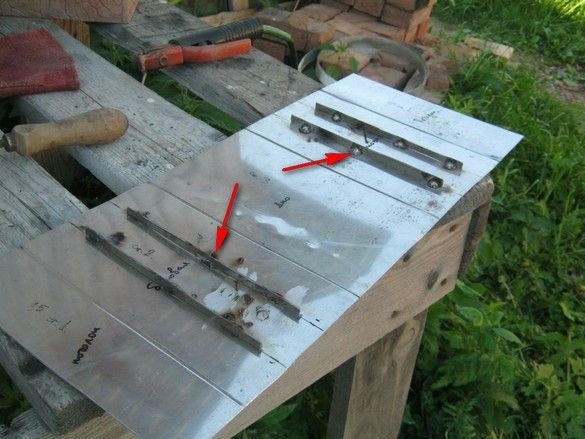
Prowadnice są przyspawane w kilku punktach na oznakowaniu. Napływy spoin powinny być skierowane w stronę potencjalnego dna, w przeciwnym razie wkładki żeliwne lub inny sprzęt będą źle włożone i osadzone krzywo.Elektrody - TsL-11, ø2mm, odwrotna polaryzacja, prąd - jeśli pamięć dobrze mi służy - 45 ... 50 A.
Należy powiedzieć, że cienkie i długie elektrody, jako spawacz od słowa „zły”, są często niewygodne - końcówka dość elastycznej elektrody zachowuje się zbyt swobodnie, dlatego w miejscach krytycznych przecięłam je na pół. Krótka połowa okazuje się znacznie szybsza i dokładniejsza, i pomimo dodatkowego zamieszania i zwiększonej straty z technologicznych „ogonów” często sięgam po tę technikę. Nie zaszkodzi też wstępne kalcynowanie elektrod - na szczęście wysokie temperatury nie będą do tego wymagane - wystarczy wulgarny piekarnik kuchenny.
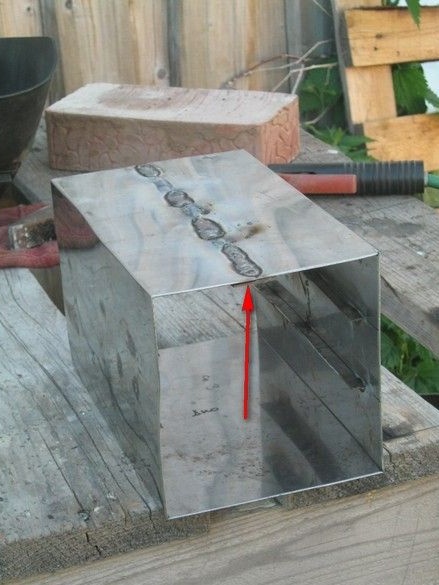
Główna część jest zgięta i spawana. Wyłożony szew spawalniczy. Specjalna szczelność mufli nie jest wymagana, wystarczy spawać „punkty” lub „linie przerywane”.
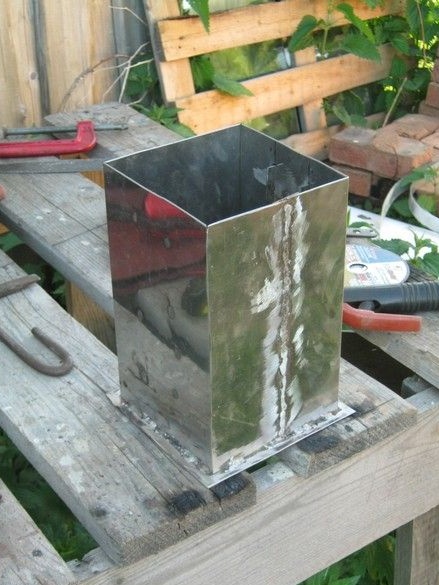
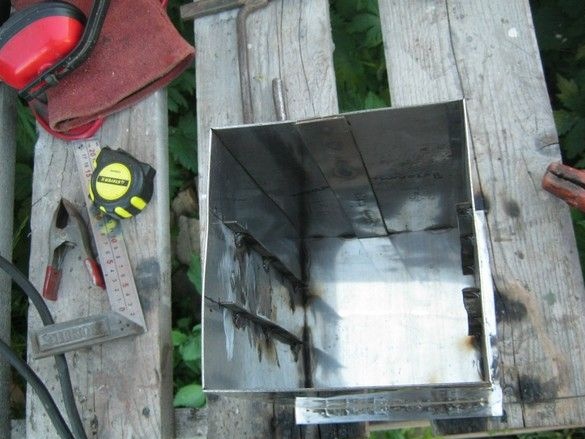
Widoczne cięcie i spawanie dna. Wygodne jest spawanie z zewnątrz, pod wieloma względami pozostaje do tego mały kołnierz o szerokości 10 mm. Jednocześnie zapobiegnie zsuwaniu się cewki nagrzewnicy. Wypaliłem dziurę na jednej ze ścian, mam nadzieję, że nie widać jej na zdjęciu.
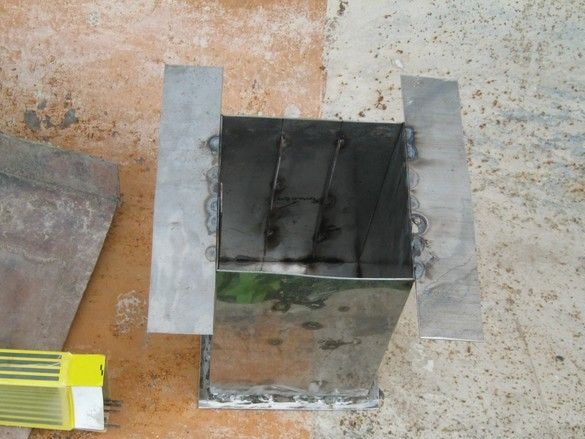
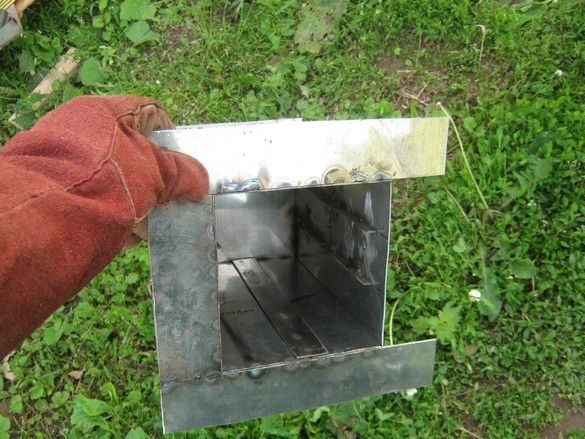
Cięcie i spawanie kołnierza zewnętrznego w kilku etapach. Najpierw wycina się cztery płyty z kilkoma - około dziesięciu milimetrów, z marginesem, a następnie dwie przeciwległe są przyspawane - długie. Następnie z kolei krótkie są regulowane i spawane, wreszcie - za pomocą magicznego „szlifierki” przycinamy całą kompozycję. Okazało się, jakby nie było źle. Tak, spawanie powinno odbywać się od wewnątrz, w przeciwnym razie trudno będzie mocno docisnąć drzwi.
Kilka słów na torze.
Metalowa mufla wymaga pewnych funkcji podczas wykonywania grzejnika drutowego. Mufla jest owinięta warstwą mokrego papieru azbestowego przed uzwojeniem grzejnika. Nawijanie odbywa się po całkowitym wyschnięciu azbestu, w przeciwnym razie drut przepchnie miękką warstwę izolacyjną.
Metalową mufę należy bez wątpienia uziemić, prawdopodobnie ma sens zasilanie grzałki z sieci za pomocą wyłącznika różnicowoprądowego (RCD) lub różnicowego wyłącznika z prądem wyzwalającym nie większym niż 30 mA.
Uzwojenie grzejnika z pewnym krokiem jest ustalone za pomocą powłoki ogniotrwałej. Trudno jest stosować płynne szkło w swoim składzie - ma pewną przewodność po podgrzaniu do wysokich temperatur.
Przykładem wykonania izolowanego elektrycznie grzejnika jest umieszczenie drutu lub spirali o wysokiej rezystancji w perełkach ceramicznych.
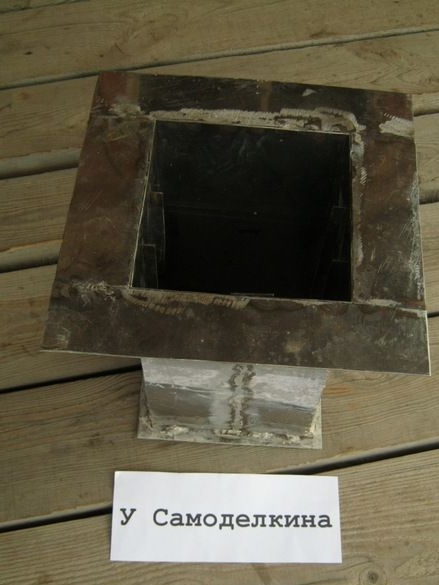
Wykaz używanej literatury.
1. Brower G. (1985) Przewodnik po syntezie nieorganicznej. T.1 Rozdział 9 Wysokie temperatury.
2. Bondarenko Yu.N. Technologia laboratoryjna. Produkcja gazowo-wyładowczych źródeł światła
do celów laboratoryjnych i wiele więcej.