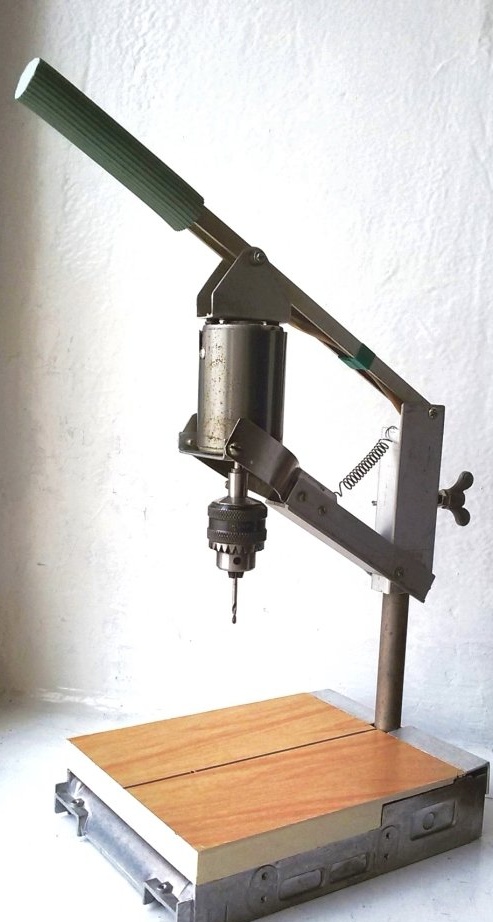
Proponuje się wykonanie małej wiertarki o bardzo prostej konstrukcji. Do jego produkcji części wzoru nie będą wymagane - precyzyjne prowadnice, łożyska toczne, mechanizmy ruchome. Jeśli w twoim domu znajduje się mały silnik instrumentu z uchwytem wiertarskim na wale, możesz rozpocząć pracę. Wykonujemy maszynę z improwizowanych materiałów. Kęsy na komponenty nie będą trudne do znalezienia.
Funkcje konstrukcyjne
Ta maszyna jest łatwa w produkcji, ale ma pewne ograniczenia. Jego konstrukcja jest przeznaczona do wiercenia otworów o głębokości do 10 mm. Możliwości maszyny w zakresie średnicy wiercenia i przetwarzanego materiału zależą od właściwości (mocy, prędkości obrotowej wału) zastosowanego silnika elektrycznego.
Ograniczenie głębokości wiercenia wiąże się z konstrukcją zawieszenia napędu siewnika. Urządzenie oparte jest na uchylnym równoległoboku. Dwa równoległoboczne pionowe, równej długości i przeciwległych ogniw, to silnik elektryczny i podstawa zawieszenia. Pozostałe dwa równe i przeciwne ogniwa to elementy łączące. Jak wiadomo, w tym projekcie przeciwne ogniwa będą równoległe przy każdym obrocie równoległoboków. Dlatego wspólna oś silnika elektrycznego i wiertarki (przy dokładnym wytwarzaniu elementów równoległoboków) zawsze będzie równoległa do osi stałego stojaka i prostopadła do stołu maszyny.
Dla porównania, romboid jest równoległobokiem, w którym sąsiednie boki mają różne długości i kąty nie są proste.
Konfiguracja i praca na maszynie.
Pozycja łączników równoległych do stołu zostanie przyjęta jako pozycja zerowa. Podczas obróbki części na maszynie, aby zwiększyć dokładność, lokalizacja tych połączeń powinna zbliżać się do pozycji poziomej.
W takim przypadku, przy osiowym ruchu wiertła od +5 mm do -5 mm (skok 10 mm) od zerowego położenia łączników, przesunięcie promieniowe wiertła (w płaszczyźnie romboidalnej) wyniesie 0,08 mm. Ta wielkość przesunięcia będzie na długości ogniwa 150 mm. W praktyce przesunięcie to jest niezauważalne i nie będzie miało decydującego znaczenia dla obrabianego narzędzia i otworu.
Podczas wiercenia płytek obwodów drukowanych, nawet przy użyciu łamliwego narzędzia z węglików spiekanych o średnicy 0,8 mm, przesunięcie wiertła na płytce o grubości 2 mm wynosi 0,003 mm (3 mikrony). Porównać podaną wartość z przesunięciem i pozycją tego wiertła podczas ręcznego przetwarzania płyt.
Ustawienie maszyny do rozmiaru części, na wysokości, odbywa się poprzez szybkie ręczne przesuwanie wzdłuż regału maszyny, podstawy zawieszenia i mocowanie za pomocą śruby skrzydełkowej. Wysokość podnoszenia i mocowania podstawy zawieszenia zależy wizualnie od ryzyka położenia zerowego (wykreślonego na podstawie zawieszenia - ostatnie zdjęcie) podczas dotykania części końcówką wiertła. Podczas wiercenia różnych desek o grubości 1 ... 3 mm nie jest wymagana ponowna regulacja wysokości.
Dodatkowe zalety konstrukcyjne.
Możliwość instalowania dużych płyt (wraz ze wzrostem zwisu wiertła zwiększa się dokładność wiercenia).
Po zwolnieniu uchwytu, pod koniec wiercenia silnik z wiertłem pod działaniem sprężyny szybko podnosi się i wycofuje na znaczną odległość, uwalniając strefę obróbki części.
W najwyższej pozycji możesz wygodnie i szybko zmienić wiertło.
Myślę, że powyższe cechy przemawiają za produkcją proponowanej maszyny. Czas poświęcony na produkcję tej konstrukcji maszyny opłaca się w dobrym nastroju, wykluczając awarie drogich i rzadkich wiertarek.
1. Obowiązujące materiały i szczegóły.
Silnik elektryczny i uchwyt mechaniczny lub tulei zaciskowej.
Kawałki blachy o grubości 1,5 ... 2,0 mm.
Wynajem profili aluminiowych, rura.
2. Wykonanie stołu wiertarki.
Przede wszystkim musisz zdecydować o stole wiertarki. Jego rozmiar, sztywność i wytrzymałość decydują o dokładności i łatwości użytkowania. Istnieje wiele różnych wzorów stołów. W danej wersji urządzenia zastosowano obudowę odtwarzacza CD, który od dawna czeka na jego wtórne użycie. Prostokątna obudowa o wymiarach 145 x 200 mm, odlewana ze stopu aluminium. Ma niską wagę, sztywną strukturę i płaskość wzdłuż obwodu dolnej części części, co zapewnia dobrą stabilność przyszłego produktu. Ponadto ta część praktycznie nie wymaga dodatkowego przetwarzania. Z tych powodów obudowę przyjęto za podstawę stołu maszynowego.
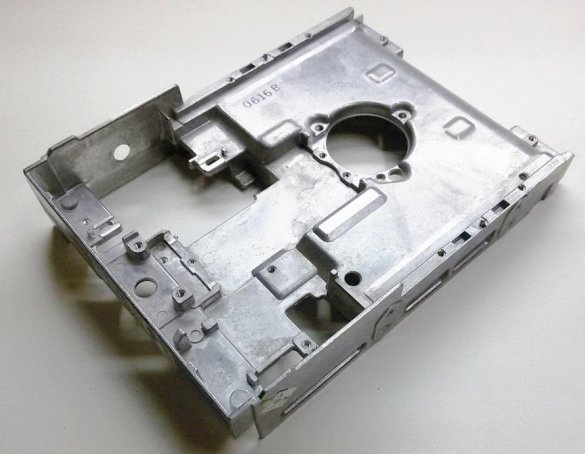
Jedna z krótkich ścian (na zdjęciu po lewej), pośrodku, ma otwór na śrubę M8, która automatycznie określa miejsce montażu stojaka maszyny.
Jako stojak można użyć walcowanego metalu lub rury o średnicy 18 ... 25 mm.
W analizowanej konstrukcji zastosowano cienkościenną stalową rurkę o średnicy 18 mm, co pozwoliło uprościć sposób mocowania jej do stołu.
Wybieramy śrubę z gwintem M8 i łbem, którego średnica ściśle wpasowuje się w otwór w rurze (może wymagać pewnego udoskonalenia średnicy). Nakręć nakrętkę na śrubę i wciśnij ją w rurkę. Stojak jest gotowy. Pozostaje naprawić go na stole za pomocą drugiej nakrętki.
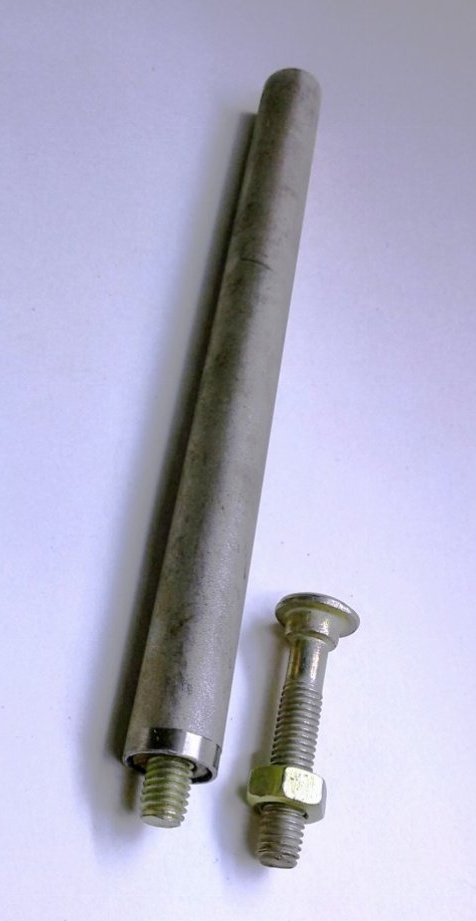
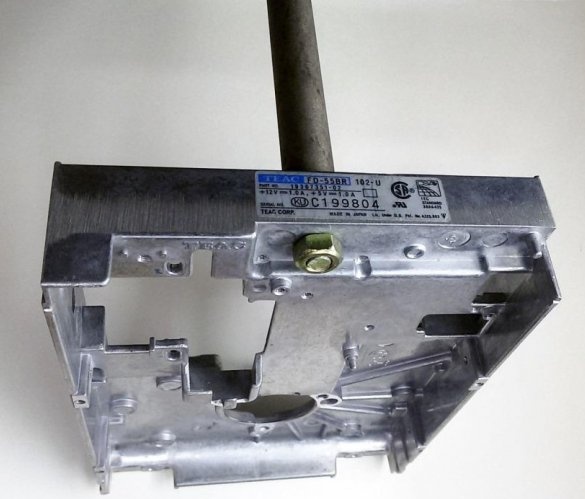
W górnej części stołu mocujemy blat wycięty z laminowanej płyty wiórowej wzdłuż konturu korpusu przedmiotu obrabianego. W takim przypadku stojak maszyny zostanie dodatkowo wciśnięty między ściankę obudowy a blat. W przyszłości po wolnych bokach regału naprawimy podszewkę aluminiowego kwadratu. Wszystko to zapewni zainstalowanej szafie dodatkową sztywność.
W trakcie tego procesu sprawdzamy i, jeśli to konieczne, dopasowujemy prostopadłość stojaka maszyny do stołu.
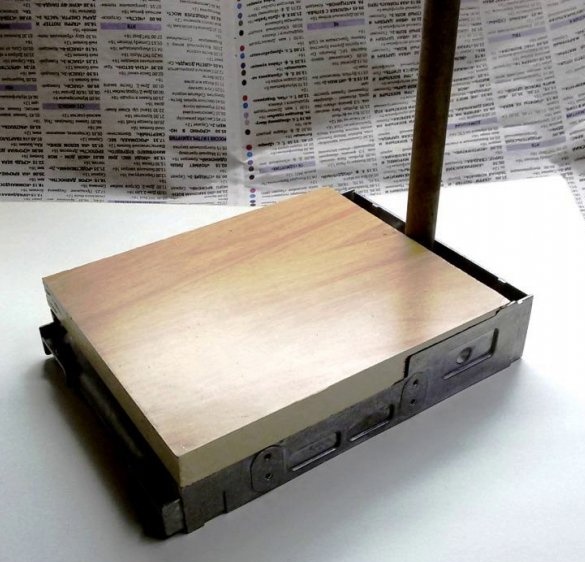
3. Podstawa zawieszenia.
Podstawa zawieszenia jest niezbędna do zamontowania przegubowego mechanizmu równoległoboku na stojaku maszyny. Służy jako integralna część romboidu, mocuje go na stojaku, na żądanej wysokości i pod wybranym kątem od krawędzi stołu. Profil aluminiowy w kształcie (18 x 40 mm), który wcześniej pełnił funkcję klamki do mebli, został wykorzystany jako blank podstawy zawieszenia.
W środkowej części profilu, około dwóch długości silnika elektrycznego, wiercimy otwór i wycinamy gwint M6 lub M8 pod śrubą mocującą. Sprawdzamy niezawodność montażu podstawy zawieszenia na stojaku maszyny.
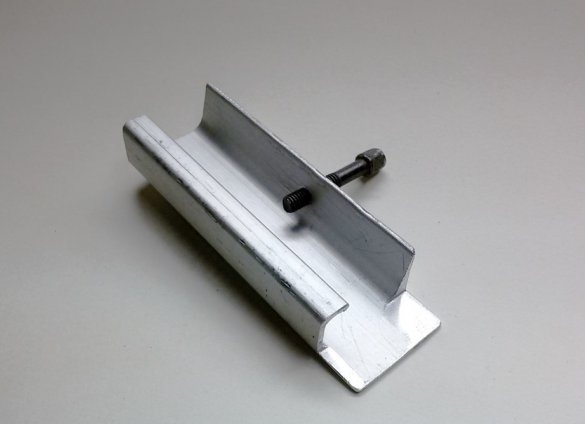
Produkcja mechanizmu do montażu silnika elektrycznego
4. Dolne zawieszenie silnika.
Do proponowanej wiertarki zastosowano silnik prądu stałego z magnesami stałymi 24 V DC, 0,7 A.
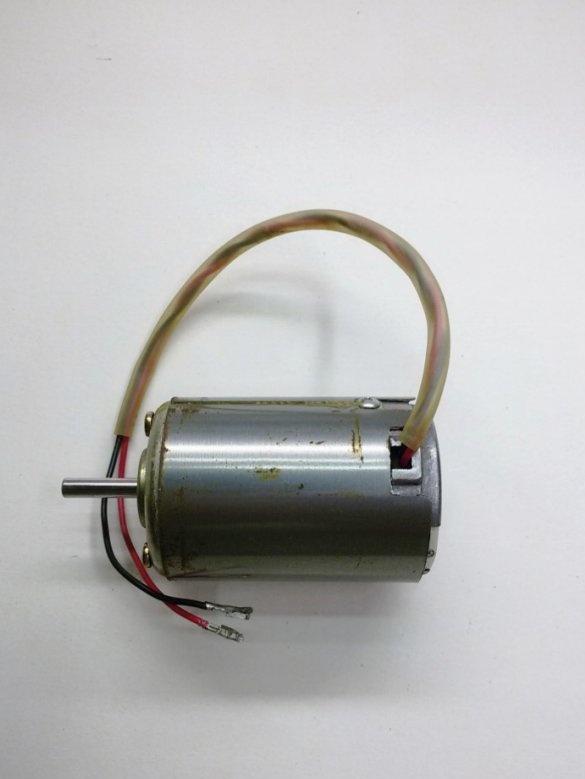
Rozpoczęliśmy produkcję przegubowego równoległoboku z łącznikiem głównym, składającym się z silnika elektrycznego i jego elementów mocujących. Wymiary zastosowanego silnika mogą być różne, a także lokalizacja otworów montażowych. Dlatego wymiary łączników nie są podane.
Z blachy stalowej o grubości 1,5 ... 2,0 mm produkujemy dolne mocowanie silnika. W bocznych półkach wspornika wywierć współosiowe otwory i wytnij w nich gwint M4. Zamontować wspornik silnika za pomocą dwóch standardowych śrub.
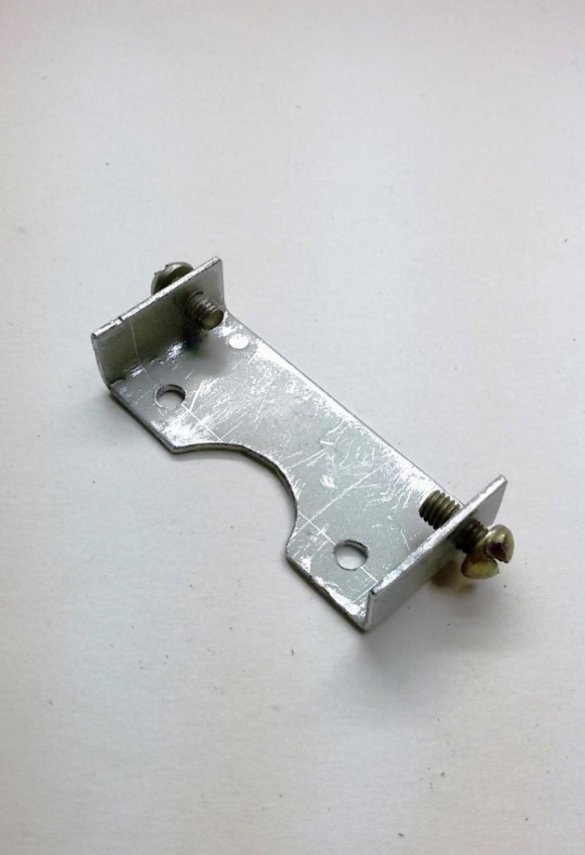
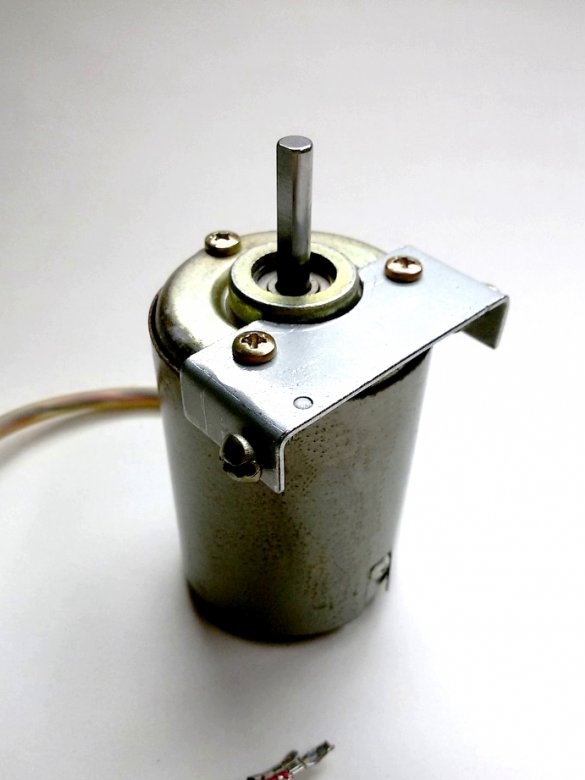
5. Dolny link równoległoboku.
Udostępnimy dolne ogniwo równoległoboku z walcowanego aluminium. Na przykład w proponowanym projekcie zastosowano profil aluminiowy w kształcie litery U (20 x 20 mm), który wcześniej był używany do produkcji okien.
Aby połączyć dolne ogniwo ze wspornikiem silnika, z blachy stalowej o grubości 1,5 mm produkujemy dwa lustrzane elementy przejściowe. Są one sztywno połączone z profilem łączącym za pomocą dwóch śrub (nitów).
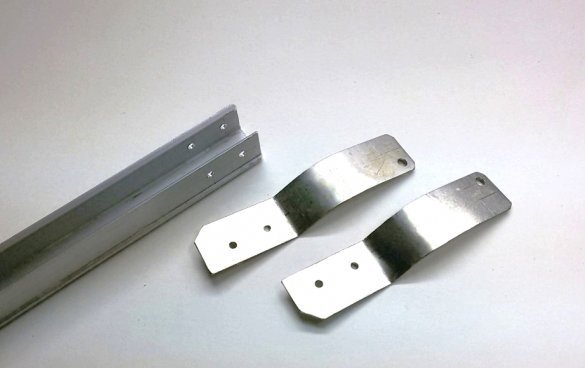
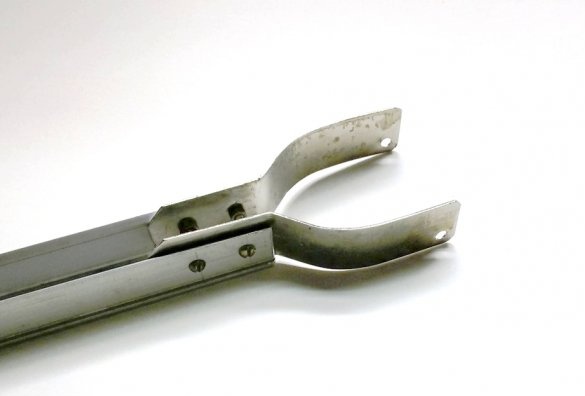
6. Dolne ogniwo ze wsparciem silnika
Długość dolnego ogniwa zależy od wielkości wyprodukowanego stołu. W tym projekcie długość ta (odległość między osiami otworów montażowych) jest zdefiniowana jako 150 mm. Zaznacz otwory do połączenia z podstawą zawieszenia i przytnij profil do żądanego rozmiaru. W razie potrzeby po wyciętej stronie profilu tworzymy szerokość rowka, aby zapewnić szczelne połączenie na szerokość z pasującą podstawą zawieszenia. Wiercimy wzdłuż oznakowanych otworów współosiowych.
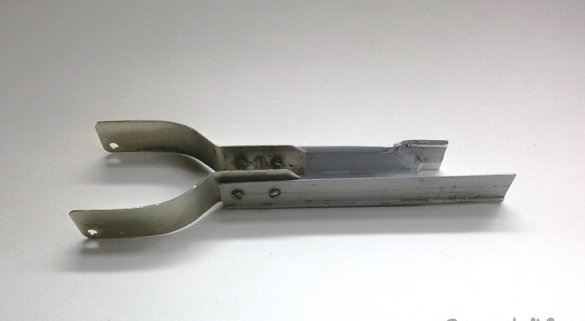
Montujemy dolne ogniwo za pomocą silnika elektrycznego. Za pomocą śrub M4 mocujemy dolne ogniwo do wspornika silnika, zapewniając swobodny obrót w połączeniu. Położenie otworu na zawiasy w dolnym ogniwie za silnikiem jest podyktowane maksymalnym możliwym wzrostem długości ogniwa, a tym samym zwiększeniem dokładności przetwarzania.
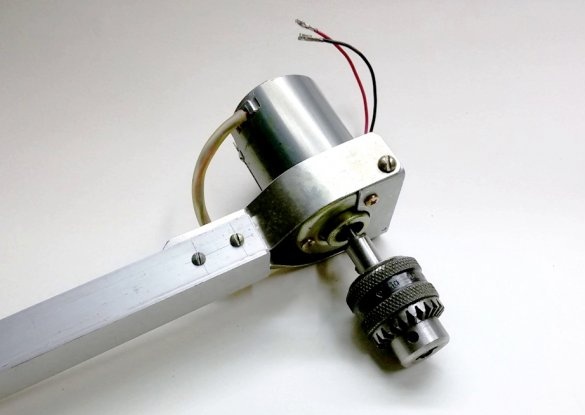
7. Górne zawieszenie silnika.
Z blachy stalowej lub aluminiowej o grubości 1,5 ... 2,0 mm produkujemy górne mocowanie silnika. Konstrukcja części będzie zależeć od położenia punktów mocowania na istniejącym silniku. Zamontować górne mocowanie silnika.

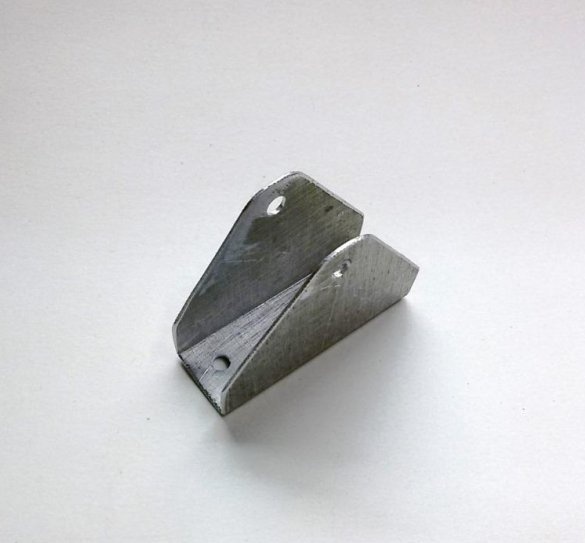
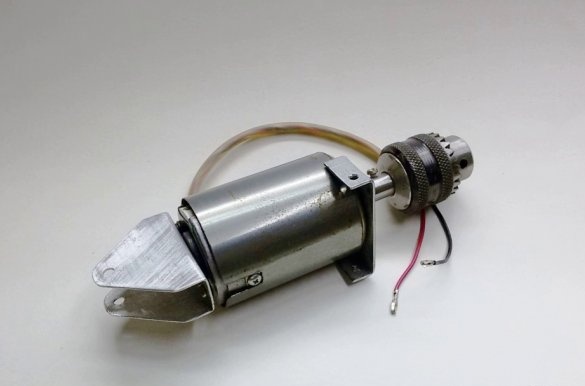
8. Górny link równoległoboku.
Górne ogniwo równoległoboku jest również wykonane z walcowanego aluminium. Na przykład w proponowanym projekcie zastosowano profil aluminiowy w kształcie litery H (12 x 16 mm). Zaznaczyć przedmiot górnego łącznika. Przenosimy odległość między osiami otworów montażowych wyprodukowanego dolnego łącznika na obrabianym przedmiocie górnego łącznika. Wywierć otwory do znakowania. Długość przedmiotu obrabianego łącznika górnego pożądane jest podwojenie w stosunku do wielkości roboczej łącznika. Wolny koniec profilu wykorzystamy jako uchwyt do podawania wiertła, co zmniejszy siłę ręki o połowę. Na tę część obrabianego przedmiotu można nałożyć kawałek plastikowej rurki.
Odległość między osiami otworów montażowych i ich umiejscowienie na wspornikach silnika przenosimy do podstawy zawieszenia. Innymi słowy, w produkowanym równoległoboku linie łączące osie otworów montażowych na mocowaniach silnika i podstawie zawieszenia muszą być równe i równoległe.
Aby spełnić ten warunek, w wyprodukowanym projekcie maszyny część profilu jest wycinana na podstawie zawieszenia (w górnej części).
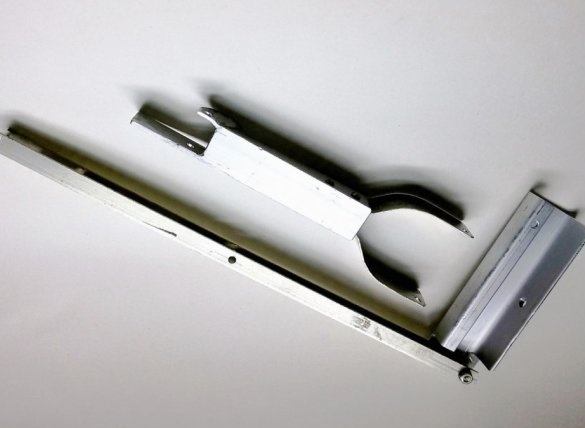
9. Montaż przegubowego równoległoboku - romboidalny.
Montujemy romboid, montujemy na stojaku i sprawdzamy działający mechanizm.
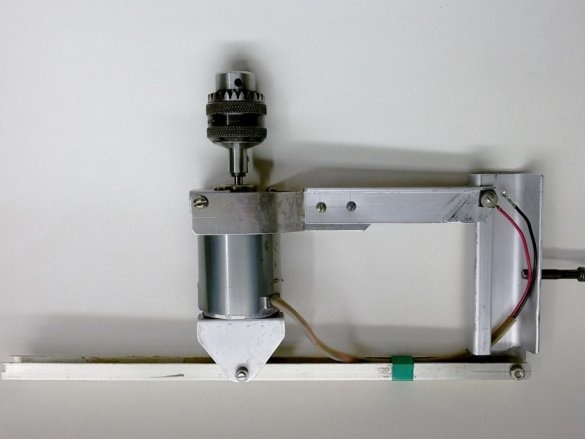

10. Kontrola dokładności mechanizmu
prostopadły
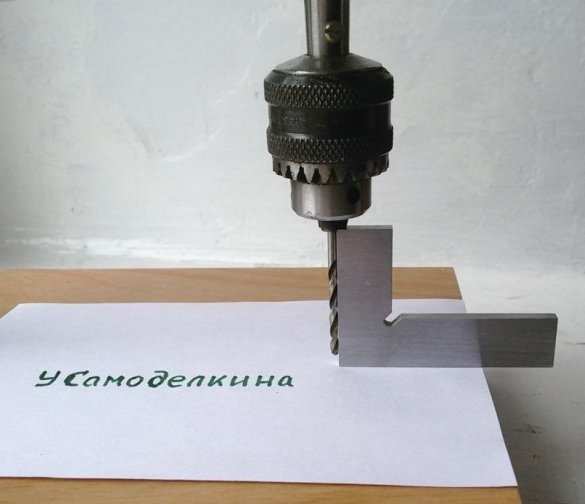
do wierteł o skoku 10 mm
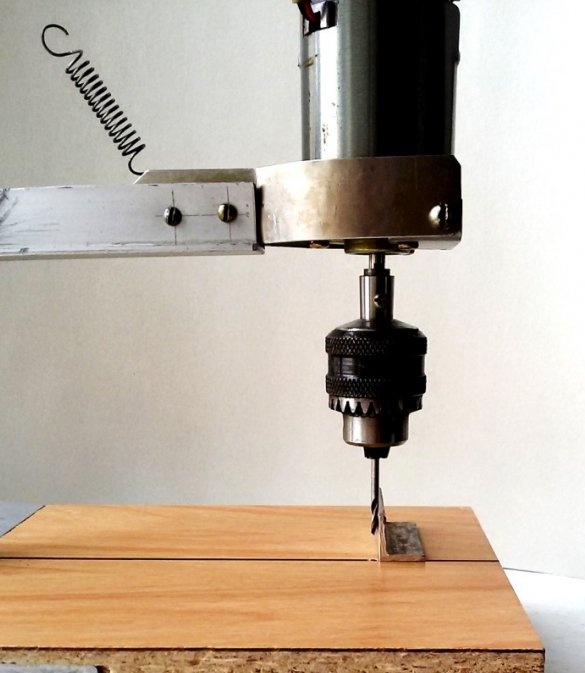
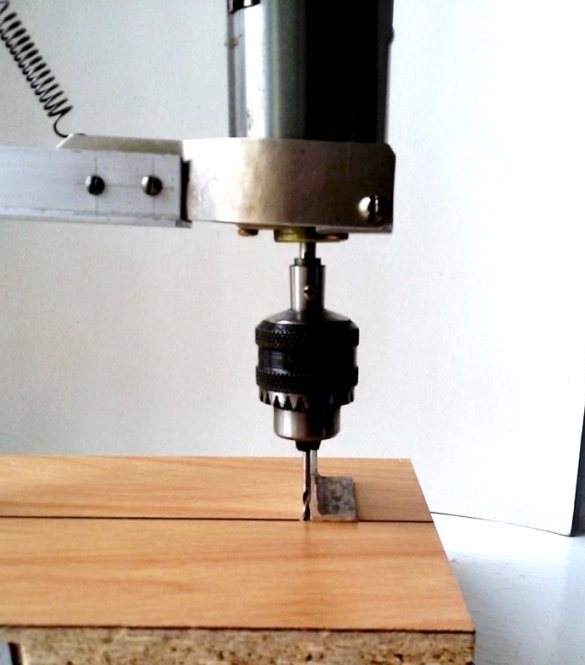
pod obciążeniem.
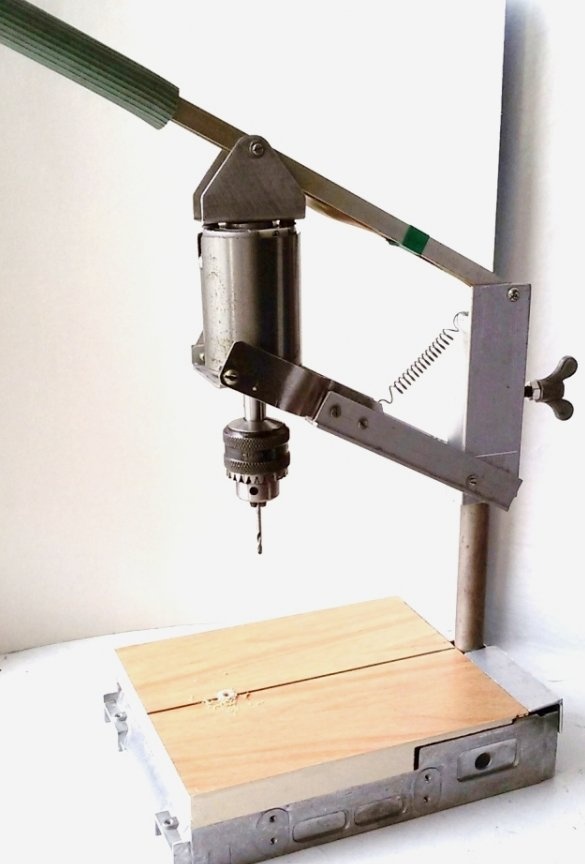