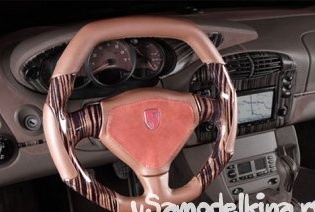
Prawe koło nigdy nie jest okrągłe. I nie jest chudy. Co więcej, bez podkładek drewnianych lub węglowych i anatomicznych stożków pokrytych perforowaną skórą. Tak wierzy wielu właścicieli tuningowanych samochodów. Dodam od siebie, że dobra kierownica ma atestowany projekt z poduszką powietrzną. Tak więc prawe koło można uzyskać przez dostrojenie fabrycznej kierownicy.
Różni eksperci ćwiczą różne metody wytwarzania wkładek i anatomii na kierownicy. Sugeruję użycie technologii matrycowej opartej na modelu gliny. Zaletą plasteliny w skuteczności poszukiwania kształtu modelu. Zaletą matrycy jest możliwość ponownego wykorzystania do produkcji tego samego steru lub fragmentów skórki dla sterów o innych rozmiarach.
Środkowa część kierownicy nie wymaga interwencji tunera; poduszka powietrzna powinna działać poprawnie. Tylko obręcz i częściowo igły mogą być ulepszane.
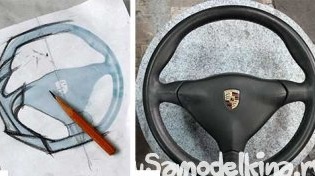
01. Konstrukcja obręczy, możesz spróbować po prostu skopiować z istniejącej kierownicy, ale możesz wymarzyć samą formę. Najłatwiejszym sposobem na wyobrażenie sobie pożądanej kierownicy jest pomalowanie konturów na obrazie steru dawcy. Ale moim zdaniem nie powinieneś długo pozostawać na papierze, ponieważ wymagania ergonomiczne i konstrukcja kierownicy mogą zniszczyć twoje niepohamowane fantazje.
02. Szczególnie miło jest ulepszyć drogą kierownicę prestiżowego samochodu, chociaż próba ręki jest warta czegoś prostszego.
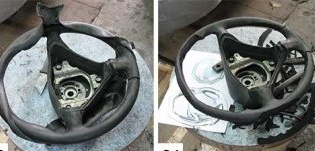
03. Większość kierownic nowoczesnych samochodów jest pokryta skórą, którą strzelam jako pierwsza. Miękka gumowa osłona obręczy otwiera się pod skórą.
04. Jeśli zdecydujemy się zmienić zewnętrzny kontur kierownicy, będziemy musieli odciąć nadmiar gumy z ramy obręczy. Ale nie angażuj się w czyszczenie ramy z gumy, lepiej zostawić ją w miejscach, w których nie przeszkadza to w zmianie kształtu.
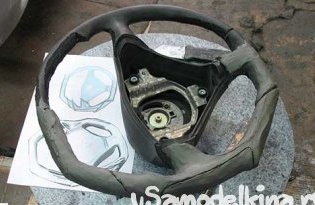
05. A teraz, w swobodny sposób, szukamy właściwych proporcji i przyjaznych dla dłoni konfiguracji kształtu na kierownicy wykonanej z plasteliny. Porównaj ergonomiczny odlew uzyskany z plasteliny z oryginalnym wzorem steru. Przenosimy charakterystyczne guzy, wgniecenia i gniazda z rysunku na plastelinę i ponownie „pompujemy” wygodę kierownicy wzdłuż ramienia.
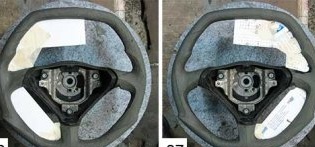
06. Z jednej strony zaczynamy opracowywać przybliżoną formę koła kierownicy. Jednocześnie odwieczny spór dotyczy tego, że najważniejsze jest plastelina lub kit, który rozwiązuję na korzyść kitu.Oznacza to, że nie wypoleruję plasteliny do lustrzanego wykończenia, aby usunąć prawie ukończoną matrycę, ale zmodyfikuję nierówności pozostawione na plastelinie na gotowej kierownicy za pomocą szpachli. Ale na plastelinie musimy zaznaczyć linie szczelinami do łatania skóry, a złamania plastikowej formy za pomocą spiczastych żeber. Z gotowej plasteliny połowy koła kierownicy wyjmij szablony z grubej tektury.
07. Kontury, linie pęknięć i krawędzie formy przenosimy przez szablony do gliny po drugiej stronie kierownicy. Boczną grubość bajgla można kontrolować suwmiarką, porównując odpowiednie miejsca po prawej i lewej stronie.
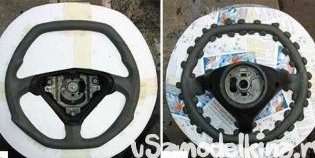
08. A teraz formularz jest zbudowany, ale nie spiesz się, aby wyrzucić szablony konturów. Z ich pomocą musimy wykonać szalunek do formowania kołnierzy łącznika półform.
Jak każda zamknięta przestrzeń, solidne koło kierownicy można uzyskać poprzez sklejenie górnej i dolnej skorupy formy. Aby wykonać te połówki z włókna szklanego, musimy najpierw wykonać formę z modelu plasteliny. Złącze wzdłuż kołnierzy podzieli matrycę kierownicy na dwie oddzielne połówki, w których łatwo jest wykonać górną i dolną skorupę samych części sterujących.
09. Szalunki kołnierzy muszą być instalowane ściśle w płaszczyźnie najszerszego przekroju wzdłużnego kierownicy. Zwykle naprawiam kartonową deskę szalunkową z kawałkami plasteliny z tyłu.
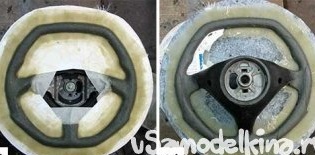
10. Praca z włóknem szklanym, a zwłaszcza formowanie kontaktowe z włókna szklanego impregnowanego żywicą poliestrową, daje praktycznie nieograniczone możliwości wytwarzania form trójwymiarowych. Materiał w stanie płynnym swobodnie otacza powierzchnie o dowolnej krzywiźnie i konfiguracji. Utwardzony kompozyt można w pełni wykorzystać zgodnie z jego przeznaczeniem. Podczas formowania szorstkich matryc zwykle nie używam żelkotów (specjalnej grubej żywicy na powierzchnię roboczą) i drogich żywic matrycowych. Przyznaję jednak, że czasami „nadużywam” zagęszczacza-aerozolu (szklanego proszku). Moja stosunkowo gruba żywica dobrze zapycha szorstkość modelu i wypełnia ostre narożniki formy. Ale na jakość formowania ma również wpływ materiał wzmacniający. Pierwsze kilka warstw, szczególnie na złożonej powierzchni, Pokrywam ją matą z włókna szklanego klasy 150 lub 300. Nie polecam nakładania wielu warstw na raz - to nieuchronnie prowadzi do deformacji włókna szklanego. Po półtorej godzinie żywica staje się stała, ale proces polimeryzacji wciąż trwa.
11. W międzyczasie pierwsza listwa spolimeryzuje, przekręcę kierownicę i wyjmę szalunek z tektury. Aby zapobiec przyklejaniu się żywicy do szalunku, uprzednio pokryłem ją woskową masą oddzielającą (teflon auto polski).
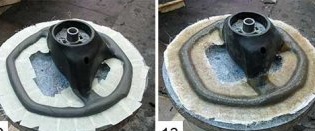
12. Kiedy nie ma pod ręką separatora, a czas nie toleruje, uszczelniam powierzchnię styku taśmą maskującą. Jest łatwo usuwalny z utwardzonego poliestru. Tym razem zamknąłem kołnierz.
13. Dolna strona modelu jest również pokryta jedną warstwą włókna szklanego. Po „podniesieniu się” żywicy, to znaczy najpierw przekształceniu jej z płynu w galaretkę, a następnie w stan stały, ponownie obracam kierownicę. Na przednią stronę modelu nakładam warstwę grubej szklanej maty klasy 600, po uprzednim oczyszczeniu poprzedniej warstwy plastiku papierem ściernym. naprzemiennie nakładając warstwy, zwiększam grubość skórki matrycy do 2-2,5 mm (co odpowiada 1 warstwie maty szklanej marki 300 i 2 warstwom marki 600).
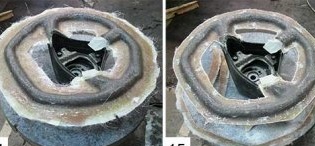
14. W pełni przyklejona matryca jest utrzymywana przez około jeden dzień, chociaż w warunkach ciągłego pośpiechu wieczorem uformowana matryca jest już rano i idzie do pracy.
15. Elastyczne i miękkie w stanie ciekłym włókno szklane, hartowanie pokazuje jego przebiegłość. Patrząc na jego powierzchnię Lollipopa, chcę ją trzymać ręcznie. Ale niewidoczne, wystające szklane igły mogą poważnie zranić twoją rękę. Dlatego przede wszystkim delikatnie czyszczę powierzchnię matrycy papierem ściernym. Kudłaty, kolczasty brzeg matrycy należy przeciąć, pozostawiając kołnierz o szerokości 25-30 mm. W odległości 10 mm od krawędzi modelu konieczne jest wywiercenie otworów montażowych na śruby w kołnierzach. W tej formie matryca jest gotowa do usunięcia.
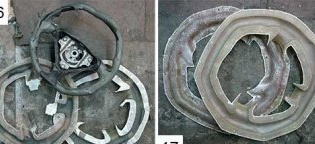
16Za pomocą ostrza noża lub cienkiej stalowej linijki rozłączamy kołnierze wokół całego konturu. Następnie rozszerzamy szczelinę utworzoną między kołnierzami i oddzielamy półformy matrycy. Cienka warstwa modelu plasteliny podczas usuwania matrycy zostaje zniszczona, częściowo pozostając w pół-formach.
17. Pozostałości plasteliny można łatwo usunąć z matrycy. Następnie wewnętrzną powierzchnię można przetrzeć naftą. Oczyszczam kontury kołnierzy papierem ściernym. Na powierzchni roboczej oczyszczonej matrycy wyraźnie widoczne są wady modelu plasteliny, co koryguję tym samym papierem ściernym.
Nawet z tą szorstką matrycą możesz zrobić kilkadziesiąt sterów. Ale kto da ci tyle identycznych kierownic do tuningu? Ale ekskluzywna praca z plasteliną i włóknem szklanym jest bardzo pożądana.
Część druga:
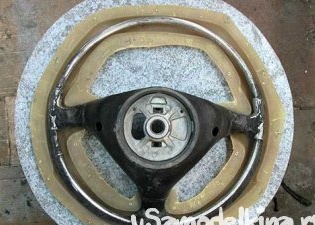
Szorstka matryca wykonana przy użyciu zwykłej żywicy poliestrowej (w przeciwieństwie do końcowej żywicy matrycowej) ma znaczny skurcz i skurcz, co prowadzi do zniekształcenia pierwotnego kształtu. Co więcej, im mniejsza i bardziej złożona część, tym bardziej zauważalne jest odkształcenie. Szczególnie silne wycofania występują w rogach, jak w naszym przypadku wzdłuż całego łuku sekcji półformy. Zatem do czasu ich całkowitej polimeryzacji widoczne niedopasowania jednej półformy względem drugiej wzdłuż konturu gromadzą się w samych częściach kierownicy. Ale do tego jest to również szorstka matryca, która ma nam pomóc w przeniesieniu pomysłu na plastelinę do półfabrykatu z włókna szklanego przyszłej formy lub służyć jako tymczasowe (niedrogie) narzędzie do badania popytu na nowy produkt.
01. Zanim zaczniesz robić połówki kierownicy, przygotowuję kierownicę do wklejenia. Stopniowo odcinając nadmiar gumy z obręczy i szprych, włożyłem kierownicę w półformę matrycy. Jednocześnie staram się pozostawić jak najmniej miejsca między obręczą a powierzchnią matrycy do sklejenia.
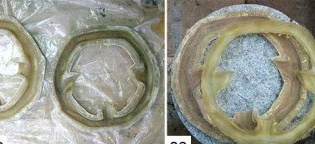
02. Skorupy na kierownicy można przykleić za jednym razem, natychmiast układając dwie warstwy szklanej maty o grubości 300 mm. Najważniejsze jest, aby spróbować utworzyć „suchy”, to znaczy usunąć nadmiar żywicy za pomocą ściśniętej szczotki.
03. Przedmiot o grubości dwóch warstw cienkiej szklanej maty okazuje się kruchy, dlatego należy ostrożnie usunąć go z matrycy. Klikam krawędzie włókna szklanego wystające wzdłuż krawędzi matrycy ku sobie i delikatnie wyciągam skórkę.
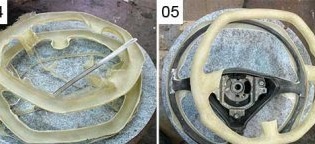
04. Nierówne krawędzie usuniętych części muszą zostać obcięte zgodnie z nadrukiem pozostawionym na części przez krawędzie matrycy. Do przycinania możesz użyć elektronarzędzia lub możesz odciąć piłą do metalu.
05. Próbuję skórki na kierownicy, przycinając w razie potrzeby gumę koła kierownicy. Aby lepiej dopasować części, wewnętrzną powierzchnię z włókna szklanego należy oczyścić grubym papierem ściernym, usuwając wystające igły z włókna szklanego i przepływy żywicy.
06. Stopniowo modyfikując krawędzie części i obręcz, dopasowuję do siebie połówki na kierownicy. Dobrze połączone i swobodnie siedzące na skórce koła kierownicy są gotowe do klejenia.
07. Istnieją dwa sposoby przyklejenia półform. Zazwyczaj części do sklejenia są wkładane do matrycy, która w stanie zmontowanym łączy je i dociska do obręczy. Ale postanowiłem zmontować kierownicę bez użycia matrycy. Chciałem sprawdzić dokładność kombinacji części i jakość wypełnienia materiałem klejącym całą przestrzeń wewnątrz kierownicy i na szwach. Jako kleju używam mieszanki żywicy poliestrowej, aerozolu (sproszkowanego szkła) i włókna szklanego. Okazuje się, że owsianka przypomina szklaną szpachlę, tylko czas utwardzania jest znacznie dłuższy. Tą kompozycją napełniam połówki kierownicy i ściskam je na obręczy. Usuwam nadmiar owsianki wyciśniętej ze szwów i naprawiam półformy za pomocą taśmy maskującej. Prawidłowo zdeformowane miejsca skorupy są korygowane za pomocą zacisków.
08. Ogrzewanie części wskazuje na intensywnie przebiegającą reakcję polimeryzacji. Półtora do dwóch godzin po rozpoczęciu klejenia usuwam taśmę klejącą i usuwam pozostałą żywicę. Następnie można obrabiać powierzchnię kierownicy.
09. Na każdej części usuniętej z matrycy są ślady warstwy rozdzielającej. Dlatego pierwszą rzeczą, którą czyszczę papierem ściernym, jest całe włókno szklane z resztek separatora.
10Tradycyjnie dostrojona kierownica jest pokryta włóknem węglowym (włókno węglowe), okleiną drewnianą i prawdziwą skórą. Masywne materiały z polakierowaną powierzchnią są umieszczane na górnej i dolnej części obręczy, a boczne części ramy sterowanej są pokryte skórą. Więc na początku planowaliśmy zrobić to na kierownicy. Ale po tym, jak trzymaliśmy w ręku prawie ukończony bajgiel, stało się dla nas jasne, że ekstremalny projekt formy wymaga niezwykłego wykończenia. Postanowiono zrobić wszystko na odwrót, to znaczy skórę powyżej i poniżej, z fornirem po bokach.
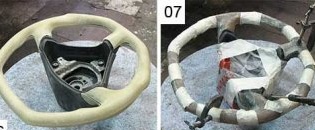
11. Dla większego komfortu pod skórą można przykleić cienką warstwę porowatej gumy (co znacznie zwiększa koszty pracy). Przybliżony kawałek nieco większy niż to konieczne jest przyklejony do obręczy kierownicy z włókna szklanego.
12. Guma ściśle przylega do obręczy. W miejscach skórzanych wstawek dłonie z gumy wycięte według jednego wzoru są również przyklejone pod dłońmi. Wszystkie fragmenty gumy są wygładzane papierem ściernym, a wady naprawiane są za pomocą okruchów gumy zmieszanych z klejem. Kontury są przycinane zgodnie z wzorami.
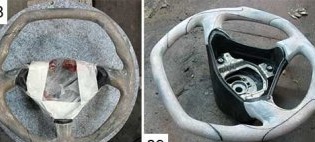
13. Kiedy planujemy zakończyć kierownicę, musisz ustawić prawidłowy stosunek wielkości obręczy na połączeniach różnych materiałów. Na przykład grubość forniru z lakierem (do 2 mm) jest równa grubości skóry z klejem. Oznacza to, że felga naszej kierownicy powinna mieć taki sam przekrój w połączeniach. Guma przyklejona pod skórą tworzyła na obręczy stopień o wysokości 2 mm. Dlatego będziesz musiał wyrównać obręcz na stawach z kitem. Aby nie popsuć krawędzi gumowych naklejek kitem, należy je zamaskować taśmą maskującą. W tym samym celu przyklejam cienki pasek plasteliny wzdłuż gumowego konturu, który stanie się szczeliną do uszczelnienia skóry.
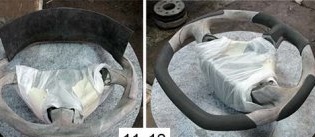
14. „Owłosiona” szpachlówka jest niezbędnym materiałem w pracy producenta pieczywa. Kit ten jest wykonany na bazie żywicy poliestrowej i dobrze miesza się z naszym włóknem szklanym z poliestru. Wiem też, że wielu rzemieślników robi kierownicę w całości z kitu. Stopniowo nakładając i szlifując kit, kierownica jest przymocowana pożądany kształt.
15. Na końcowej powierzchni kierownicy zaznaczam linie pęknięć, aby uszczelnić skórę. Cięcia na feldze najwygodniej wykonuje się za pomocą metalowego ostrza do metalu. Głębokość szczeliny powinna wynosić co najmniej 3-4 mm, a szerokość do 2 mm. Cięcia wykonałem szmatką z papierem ściernym. Szczeliny wkładek pod dłońmi zostały oznaczone paskami plasteliny. Po usunięciu plasteliny rowki są wyrównane z kitem i papierem ściernym. Bardzo wygodne jest układanie szczelin „maszyną borową”.
16. Ostatnim akcentem jest instalacja i montaż osłony poduszki powietrznej. Najważniejsze jest prawidłowe obliczenie luk. Faktem jest, że ruchoma osłona nie powinna ocierać się o krawędzie ramion. Ponadto musisz zostawić miejsce na grubość skóry lub Alcantary, która zakryje poduszkę powietrzną.
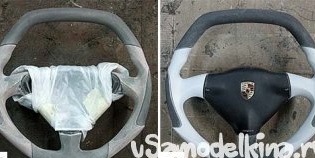
Dla dokładności dopasowania wkładam kawałki skóry do szczeliny i „pompuję” właściwe miejsce. Aby dopasować szczeliny, stosuje się wszystkie te same środki - kit i papier ścierny. Kończę włókno szklane podkładem, aby pojawiła się cała forma, ponieważ trudno jest zobaczyć nierówną powierzchnię z kitu wady
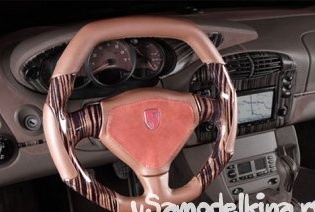
To kończy pracę prototypu, a produkt jest wysyłany do innych specjalistów. Najpierw jeden mistrz wklei fornir i lakieruje go, a następnie inny mistrz pokryje go skórą. Ostateczny wynik będzie zależeć od kwalifikacji finiszerów, ale mistrz układu dzięki ergonomii, plastyczności i proporcjom będzie układał mistrza układu. Dlatego podstawową specjalizacją w wytwarzaniu niestandardowych produktów była zawsze produkcja makiet.