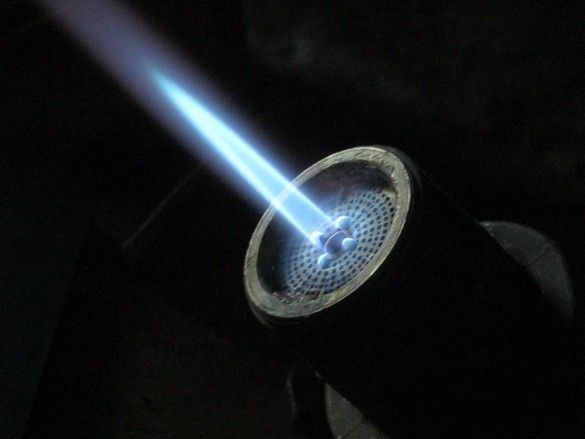
Palnik stołowy jest głównym narzędziem do szkła, niezależnie od tego, czy jest to szklany instrument, czy zabawne figury i dekoracje. Palnik tworzy płomień, wygodny do zmiękczania szkła i kolejnych operacji z nim. W takim przypadku konieczne jest uzyskanie różnych temperatur i form latarki.
Przez przypadek dostałem małą pochodnię ze szklanym blatem, tworząc raczej cienką, nieuregulowaną igłę płomienia. Nawet podczas pracy na oparach benzyny (temperatura płomienia jest wyższa niż temperatura płomienia gazowo-powietrznego) moc palnika nie była wystarczająca do pracy z tak dużymi przedmiotami. Dla pewnego wzrostu strumienia ciepła skompilowano dwa palniki - dodano przenośny gaz w przeciwnym kierunku lub w podobny sposób.
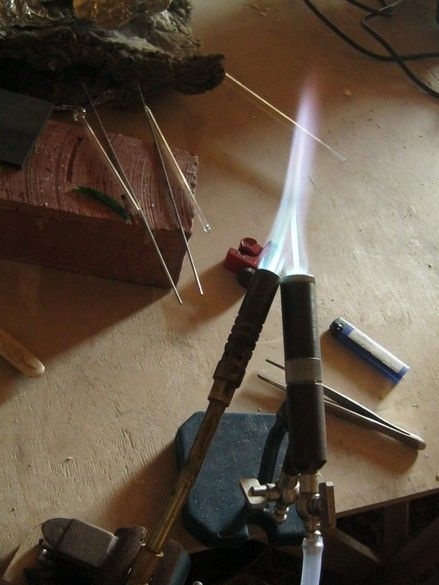
Okazało się puszysty płomień z igłą wysokotemperaturową pośrodku. Sprawy stały się przyjemniejsze, stało się możliwe napompowanie rury 10 mm. Kolejnym logicznym krokiem było wyprodukowanie mocniejszego palnika spalającego opary benzyny.
Będzie to prototyp palnika wykonanego z improwizowanych materiałów - są to głównie elementy hydrauliczne. Części obrabiano bez metalowej tokarki. Palnik działa na oparach benzyny i jest oparty na dmuchawie szkła Jurij Nikołajewicz Bondarenko [1], dmuchawie szkła-astronomie produkującym urządzenia wyładowcze. Rozwiązania niektórych jednostek zostały zapożyczone z jego projektu, w przeciwnym razie palnik powtórzy projekt znany jubilerom i dentystom.
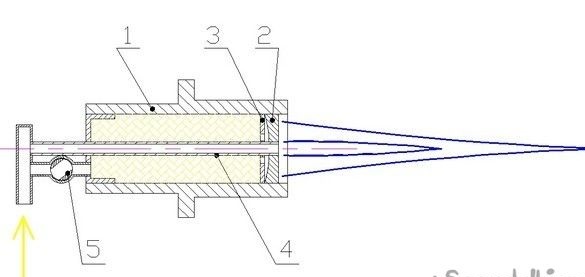
Jego podstawą jest wydrążony cylindryczny korpus 1, współosiowy, przez który przechodzi dysza 4. Kran kranowy 5 umożliwia dostosowanie kształtu palnika - po otwarciu część palnej mieszanki wchodzi do korpusu oprócz dyszy i jest formowana w palniku przez kratkę 2. Przysłona 3, w połączeniu z kształtem kratki 2 i wynikowej wnęki soczewkowej koncentruje przepływ palnej mieszaniny głównie wzdłuż osi palnika. Te części są zapożyczone z palnika mentora [1]. Na rurze dyszy znajduje się kilka otworów dostarczających niewielką ilość gazu do siatki (nie pokazano na szkicu) oraz z całkowicie zamkniętym kranem 5, aby utworzyć małą pochodnię podtrzymującą.Nie pozwala na pęknięcie głównego palnika - „igły” przy dużych prędkościach przepływu gazu. Otwory te są wybierane podczas ustawiania palnika.
Narzędzia, sprzęt.
Lut miękki wymaga małego palnika gazowego. Zestaw narzędzi stołowych. Ostrzałka elektryczna. Zastosowano tokarkę do drewna i wiertarkę. Imadło
Materiały
Oprócz elementów żelaznych potrzebna była rura miedziana o średnicy 6 mm. Lut cynowo-miedziowy nr 3, topnik do niego. Kran korkowy z samowara.
Półfabrykat korpusu palnika był fabrycznie wykonanym z brązu łącznikiem ze sklepu hydraulicznego o wewnętrznej średnicy 30 mm. Zakupiono tam również kilka różnych części, z których niektóre wykorzystano później jako półfabrykaty na elementy palnika.

Jedno z łączników służy jako obudowa bez zmian. Oprawa nie została odwrócona na zewnątrz - duża grubość ścianek i pływy zapewniają ciału dodatkowe odprowadzanie ciepła.
Rozmiar zaślepek hydraulicznych został tak dobrany, aby przy minimalnym skręceniu gwintu uzyskana część pasowała do wewnętrznego kanału łącznika. Szlifuję drewno na tokarce, w tym celu obróciłem prosty zatrzask, na którym posadziłem przedmiot.
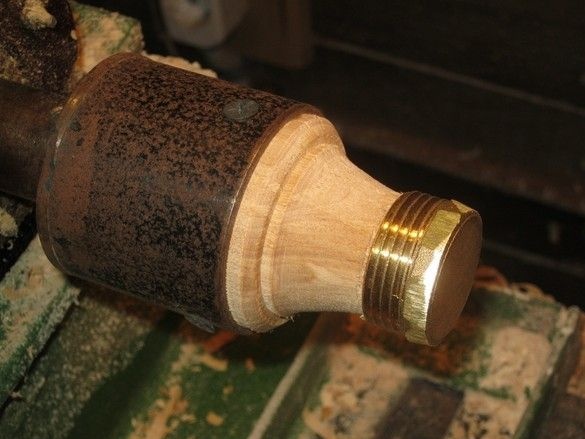
Gęstość lądowania pozwoliła na więcej, nie ma sposobu, aby naprawić część. Silnie wchodzące w narożniki sześciokąta „pod klucz” są wcześniej szlifowane na szlifierce. Obroty - około 1000 obr / min, pierwsze zgrubne toczenie z małym „szlifierką” - część obraca się, szlifierka działa. Po zakończeniu pilnika i środkowej skóry przypiętej do drewnianego klocka. Końcowe zamocowanie przedmiotu obrabianego umożliwiło wygodne i często przymierzanie go do „miejsca pracy” - uzyskana część wchodzi szczelnie do obudowy przy niewielkim wysiłku.
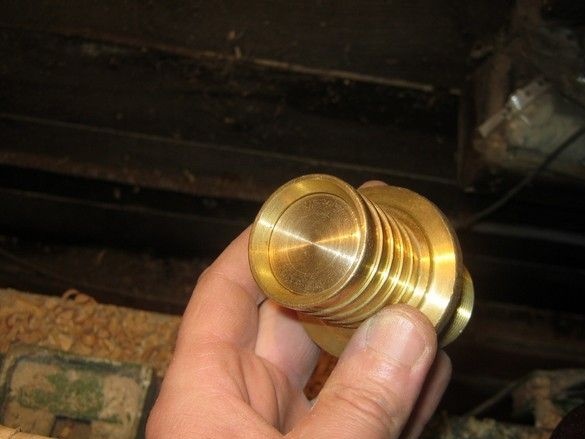
Przechodzimy do złożonego i kluczowego szczegółu - siatki. Najpierw kilka rozważań teoretycznych.
Siatka, oprócz dystrybucji mieszanki gazów palnych, jest również odpowiedzialna za bezpieczeństwo - nie pozwoli, aby płomień przedostał się do środka i uniknął „uderzenia wstecznego”. Dzieje się tak, ponieważ nasza mieszanka paliwowa jest przygotowywana balon „bulwa” i nie jak zwykle - w miejscu palnika. W tego typu palniku do pełnej pracy ze szkłem, w tym ze szkłem ogniotrwałym, takim jak Pyrex, konieczne jest dodanie gazu wybuchowego z elektrolizera.
Płomień, przechodząc do środka, przez siatkę, ochładza się tak bardzo, że gaśnie. Istnieje koncepcja - ostateczna dziura. Jest to maksymalna średnica „głębokich” otworów zdolnych do wykonywania funkcji tłumienia płomienia i jest różna dla różnych gazów. Na przykład w przypadku oparów benzyny w powietrzu, których prędkość rozprzestrzeniania się płomienia jest niewielka, otwór ograniczający wynosi ~ 0,9 ... 1 mm, ale gdy tylko tlen lub gaz wybuchowy wnikną do układu, co znacznie zwiększa prędkość rozprzestrzeniania się płomienia, otwory w „siatce ochronnej” będą musiały zostać znacznie wykonane mniej Maksymalna średnica otworów, na przykład dla czystego gazu wybuchowego, ~ 0,3 mm, co stanowi pewną trudność w produkcji i działaniu.
Jako rodzaj kompromisu Jurij Nikołajewicz proponuje wykorzystanie otworów w siatce 0,8 mm, a niezbędnym środkiem bezpieczeństwa w warsztacie będzie dość solidna konstrukcja „żarówki” i „płukania” elektrolizera [1], aby mogli przetrwać ewentualny wybuch bez uszkodzeń. Gaźnik benzynowy wykonany jest z cylindra propanowego, który myje elektrolizer z gaśnic na dwutlenek węgla. Podczas normalnej pracy urządzenia nie dochodzi do przełomów. W przypadku naruszenia normalnych warunków pracy dochodzi do klaśnięcia, które nie prowadzi do wypadku.
„Długość” otworów siatki daje jej grubość. Biorąc pod uwagę kształt soczewkowy, grubość siatki powinna wynosić 3 ... 4 mm w cienkiej części i 6 ... 7 mm na krawędziach. Nie było gotowego talerza o takiej grubości; musiałem szukać dawcy. Okazało się, że jest to dość masywny, przestarzały kran do łazienki. Wycięto z niego względnie równy fragment ściany, z którego można było wyciąć półfabrykat do siatki.
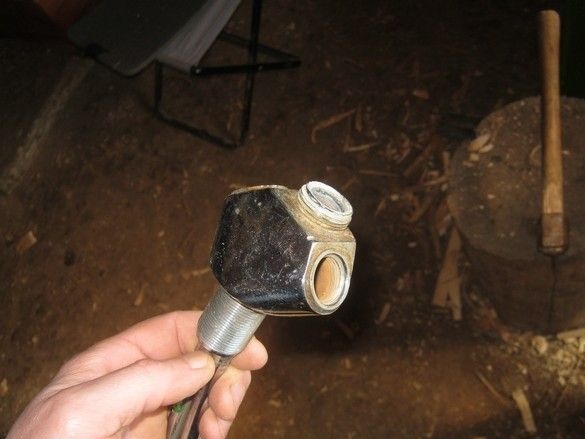
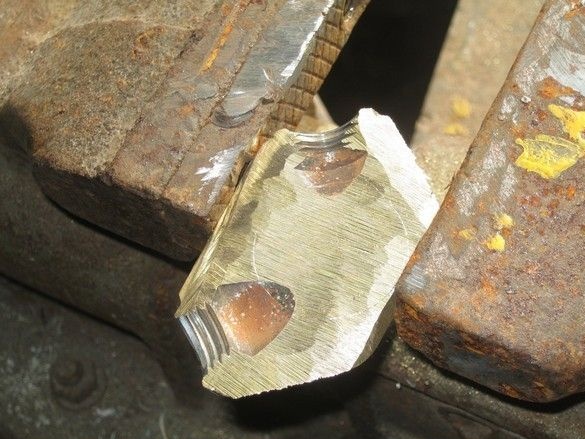
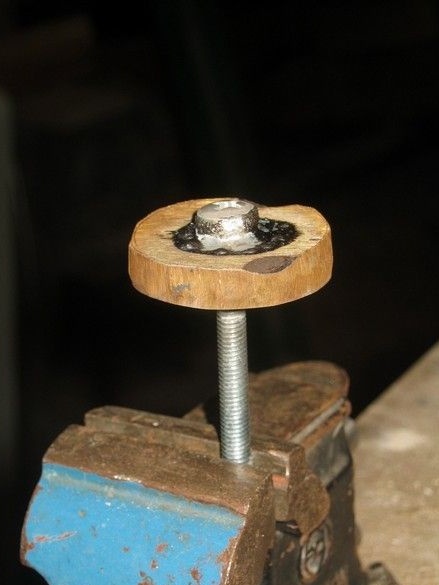
Obrabiany przedmiot, po zgrubnym toczeniu, został zamontowany (lutowany) na śrubie M5, do której można zamocować obrabiany przedmiot w trzyszczękowym uchwycie w celu dostosowania rozmiaru i kształtu.
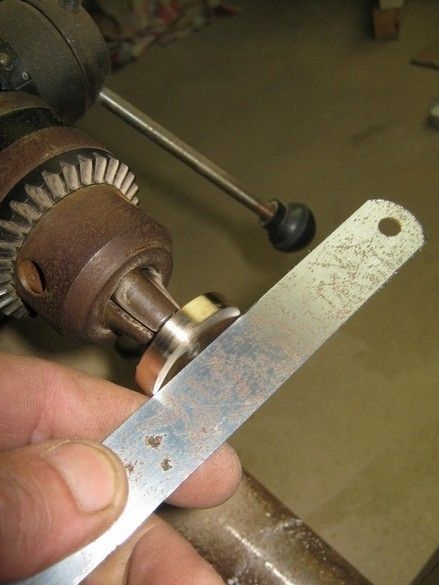
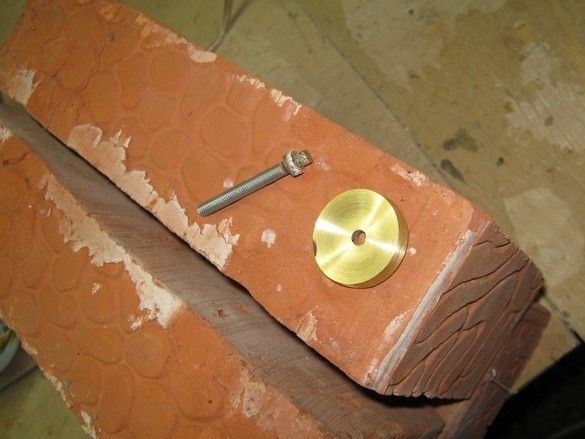
Wiertarka, dla łatwości obsługi została położona na boku. Wklęsła powierzchnia obrabianego przedmiotu została obrabiana zgrubnie - małym „szlifierką”, „resztką” tarczy (mniejszy promień), a następnie sprowadzona piaskiem szlifierskim. Śruba jest przylutowana, więc wystająca głowica została oszlifowana wraz z przedmiotem obrabianym. Następnie zewnętrzna średnica przedmiotu obrabianego została doprowadzona do pożądanego. Po obróceniu stopiłem trzon z przedmiotu obrabianego - pozostałą część śruby M5. Pozostały otwór został wywiercony do pożądanego 6 mm.
Kolejnym odpowiedzialnym i raczej ponurym etapem jest przechylenie centrów przyszłych otworów i wywiercenie ich. Przy odpowiedniej liczbie otworów i ich średnicy zadanie nie jest łatwe. Doświadczenie amatorskiego radia bardzo pomogło - wybijanie i wiercenie dużej liczby otworów w elementach płytek drukowanych przed wynalezieniem komponentów bezołowiowych (SMD) było powszechną praktyką.
Średnica otworów została już omówiona, należy powiedzieć o ich liczbie - ich całkowita powierzchnia powinna wynosić co najmniej 20% powierzchni siatki.
Wygodnie jest rysować dziury w programie AutoCAD, między innymi ten program pozwala wydrukować szkic dokładnie w skali 1: 1. Po wydrukowaniu powstały szablon przyklejono do płaskiej powierzchni siatki za pomocą kleju-ołówka, koncentrując się na środkowym otworze, wygodnie jest to zrobić w świetle.
Do wkręcenia użyłem specjalnego miniaturowego rdzenia. Powinieneś zadbać o dobre jasne światło, specjalny daszek z lupami jest wygodny do tej pracy. Praca nie jest szybka i ważne jest zorganizowanie wygodnego miejsca - pewnej wolnej powierzchni, „operatora” w pozycji siedzącej. Polecam wykonywanie takich operacji w więcej niż jednym podejściu. Po wykrawaniu szablon złuszcza się, a pozostałości zmywa się ciepłą wodą.
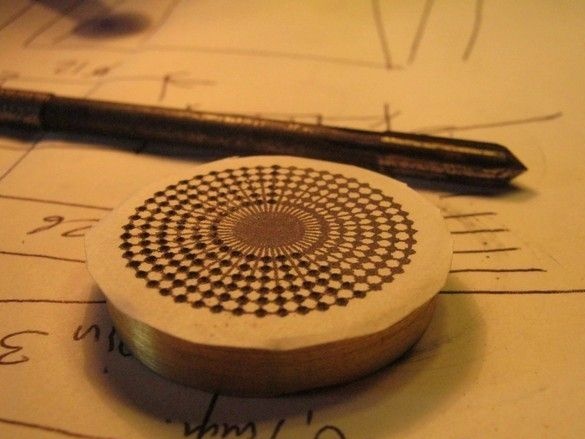
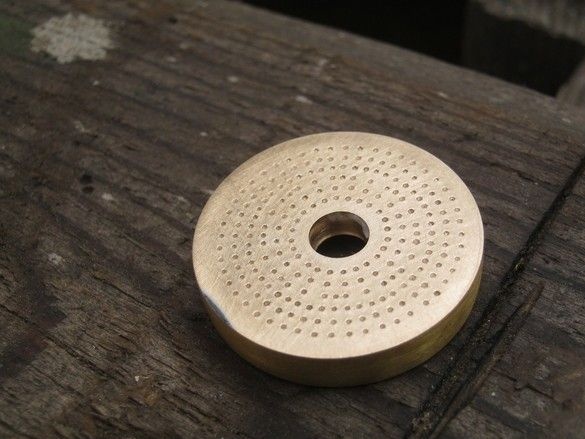
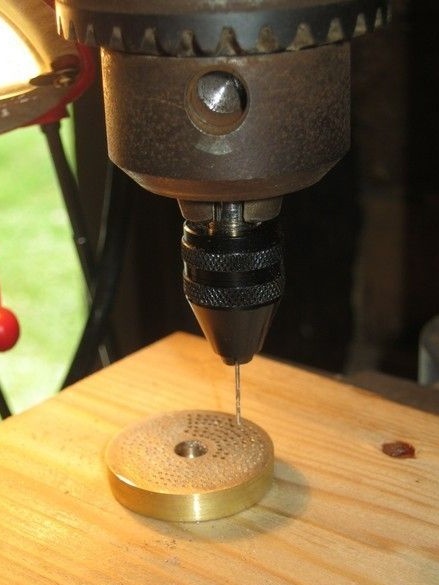
Do wiercenia tego rodzaju - gruby metal, cienkie wiertła, niezbędna dokładność, różnorodne urządzenia ręczne nie mają zastosowania. Powinieneś użyć czegoś bardziej stacjonarnego. W tym przypadku do zamocowania wiertła 0,8 mm użyto miniaturowego uchwytu wiertarskiego; uchwyt wiertarski zamocowano w dużym uchwycie trójszczękowym na wiertarce stołowej. Ta kombinacja pozwoliła nam pewnie wiercić cienkim wiertłem; złamałem tylko jeden, a nawet wtedy na samym końcu.
Okazało się, że są to niedrogie wiertła zakupione w sklepie radiowym i były one złej jakości, co stanowi rodzaj uproszczenia w stosunku do pomysłu wiertła. Rowki do odprowadzania wiórów były na nich bardzo płytkie. Podejrzewa się, że są one wykonane specjalnie do wiercenia w folii z włókna szklanego i lepiej jest używać zwykłych wierteł „do budowy maszyn”.
Jurij Nikołajewicz mówi, że zdarzają się przypadki wiercenia podczas głębokiego wiercenia, więc należy je kupić z marginesem, a następnie nie wybierać klinów. Zakłada się, że jest to spowodowane ich stożkiem. Wiercenie jest nieco łatwiejsze podczas smarowania wiertła olejem lub alkoholem, ale alkohol należy stale dodawać.
Prawidłowe ostrzenie takiego miniaturowego wiertła jest trudnym zadaniem, a przy braku umiejętności lepiej jest używać nowych wierteł, w przeciwnym razie znaczące „pociągnięcie” jest nieuniknione podczas wiercenia. Jednak przy starannym wierceniu w maszynie wszystkie niezbędne otwory można wiercić jednym wiertłem z jednego ostrzenia.
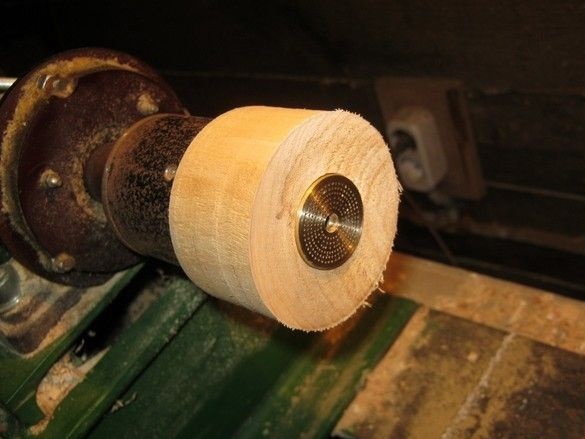
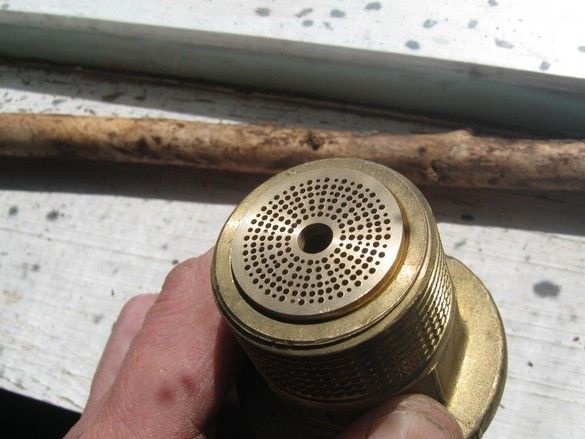
Po wierceniu wszystkie powstałe małe zadziory należy przeszlifować. Najwygodniej robi się to na części obrotowej. Aby zainstalować siatkę w tokarce do drewna, obrabiano najprostsze urządzenie. Siatka ściśle przylega do wnęki.
Podczas produkcji prototypowego palnika miał on działać tylko na opary benzyny, więc niektóre otwory były większe - 1 mm.
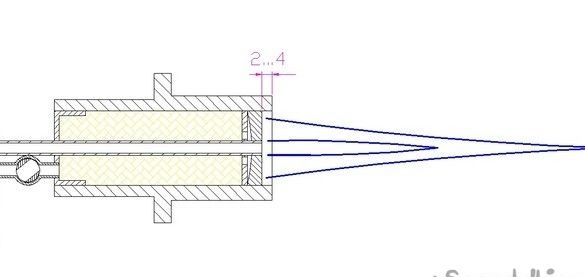
Kratka jest wpuszczona w korpus o 2 ... 4 mm. Jurij Nikołajewicz zaleca ostrożne wybranie tego rozmiaru - jeśli występuje nadmiar, korpus palnika nagrzewa się bardzo, jeśli nie jest wystarczający, latarka w niektórych trybach jest podatna na awarię.
W moim „niskotemperaturowym” przypadku - karmiąc tylko opary benzyny, bez gazu wybuchowego i przy bardzo masywnej obudowie, ustawiam maksymalną głębokość bez strojenia. Później fajnie byłoby przylutować siatkę. Należy tego dokonać za pomocą „twardego” lutu. Miedź-fosfor jest odpowiedni, ale w tym przypadku srebrny lut, taki jak PSR-45, jest lepszy, mniej się wypala. Nie mogłem w pełni wlutować siatki w moją masywną skrzynkę, nie mogłem wlutować jej lutem - nie było wystarczającej temperatury, nawet gdy ogrzałem ją odbłyśnikiem, dużym palnikiem. Jednak siatka weszła w ciało z dobrym dopasowaniem, więc zostawiłem ją taką, jaka jest.
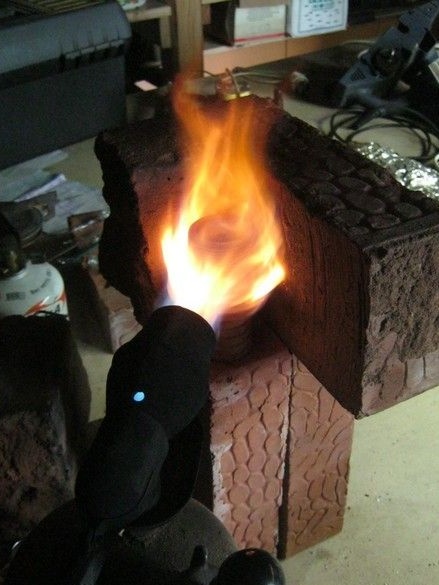
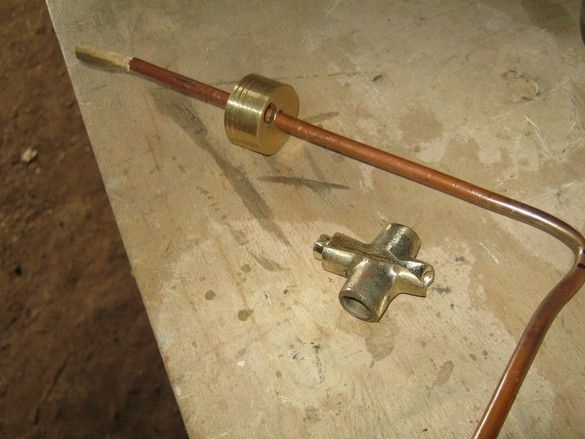
Dysza - pełne uproszczenie. Wykonany z rurki miedzianej o średnicy wewnętrznej 4 mm. Użyj tylko jako opcji próbnej. Zacytuję z [1] - „Dysza powinna dawać wąski laminarny przepływ palnej mieszanki i ostrą pochodnię przynajmniej o niskim płomieniu. Jego laminarność można zapewnić dzięki średnicy otworu do 2,5 mm, długości większej niż 35 mm, polerowanej powierzchni wewnętrznej i spokojnemu przepływowi na wlocie. Płomień laminarny wytwarza mniej hałasu i pozwala zmniejszyć strefę grzewczą, dlatego powinieneś spróbować zdobyć pochodni laminarną. (Profesjonalni dmuchacze szkła mogą mieć różne opinie na ten temat). Otwór dyszy najlepiej jest wykonać stożkowo - zapewni to mniejszy opór przepływu. Część końcowa o długości około dziesięciu milimetrów powinna być cylindryczna. ”
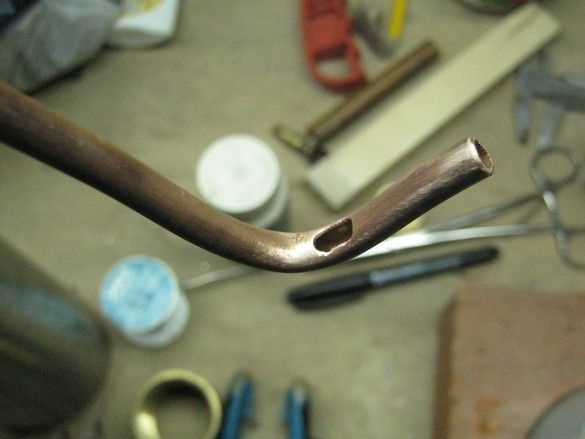
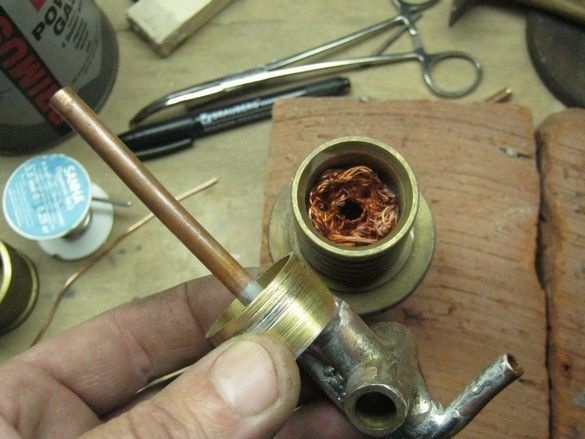
Przed gięciem rurkę dyszy wyżarzono i wypełniono suchym piaskiem. Wewnętrzna komora palnika została luźno wypełniona bez specjalnego fanatyzmu miedzianym „mętlikiem” - jest to dodatkowa ochrona przed „przebiciem” płomienia i uspokojeniem przepływu gazu. Wypełnienie utrzymuje również przeponę dociśniętą od środka do kratki.
Całe lutowanie „z tyłu” jest wykonane przez lut cynowo-miedziowy o temperaturze topnienia około 200 ° C. Korpus palnika znacznie się nagrzewa, część tylna nie jest wyższa niż 60 ° C - można go łatwo chwycić ręcznie, a nawet po dłuższym użytkowaniu urządzenie się nie zapada.
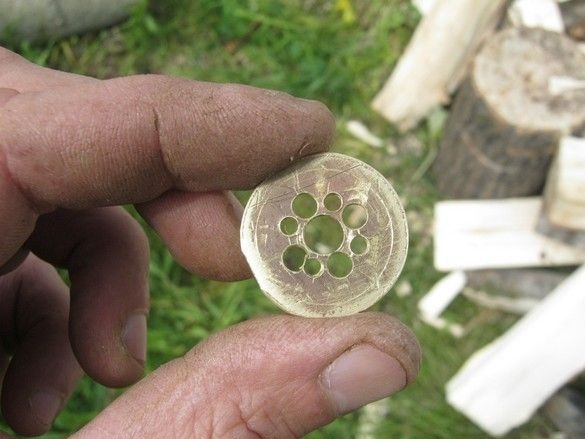
Sama membrana jest wykonana z płaskiej mosiężnej płyty o grubości 3 mm. Aby uzyskać wyraźniejszy efekt, „soczewka” powinna być dwuwypukła, dla której przesłona powinna być również wklęsła. Aby to zrobić, można go wygiąć za pomocą Punzel i Ankilub szlifuj z grubszego przedmiotu podobnego do siatki.
Po próbnych zapłonach wydawało się, że latarka jest krótka, co prawdopodobnie spowodowało, że widoczne były cienkie odcinki rur dostarczających gaz do obudowy. Palnik został zmodernizowany - kanały korkowe są wiercone do średnicy 7 mm, wymieniono wspólną rurkę zasilającą.
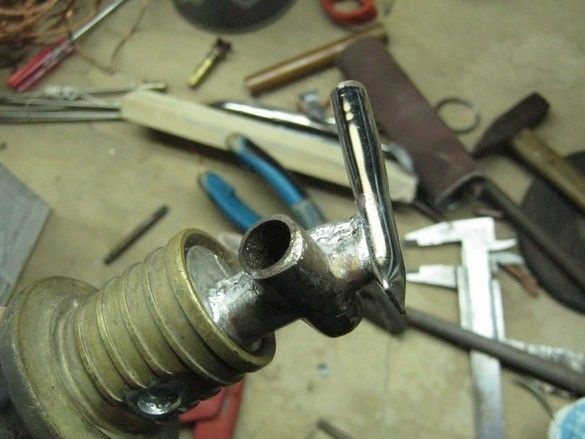
Było trochę lepiej. W tym samym czasie ustawiłem pochodnię. Jurij Nikołajewicz zaleca umieszczenie trójkątnego pliku rowków, rodzaj gwiazdki o pięciu do siedmiu promieniach, w otworze w siatce, przez który przechodzi środkowa dysza, tak aby wokół dyszy wzrósł przepływ mieszanki. Zwiększy to stabilność „igły” i zmniejszy przeciągnięcie w trybie turbulentnym.
Ilość palnej mieszanki dla płomienia podtrzymującego jest ustalana przez otwory w dyszy wewnątrz obudowy. Ich liczbę i rozmiar można dostosować.
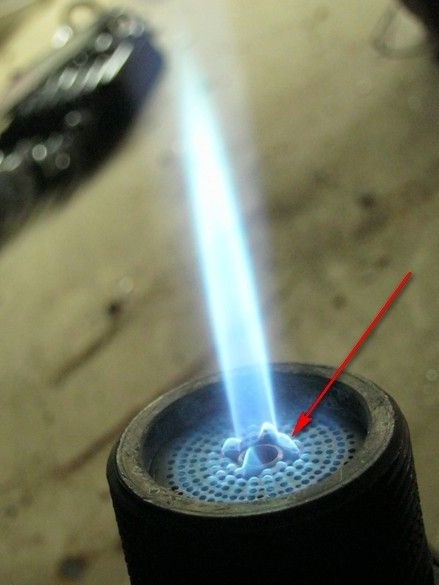
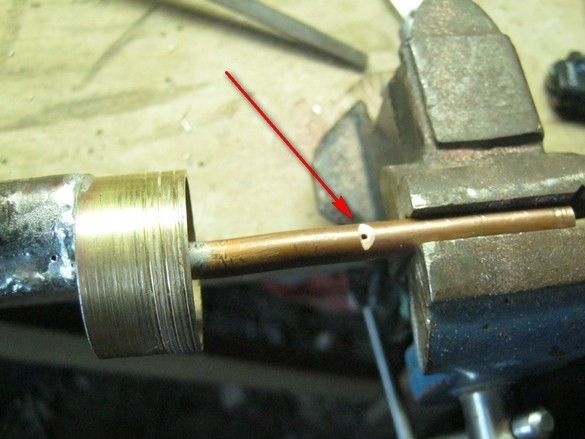
Kilka zdjęć pochodni uzyskanych do tej pory z różnymi pozycjami kranu na palniku - że tak powiem, „igła”, „miękki” płomień i coś pomiędzy.
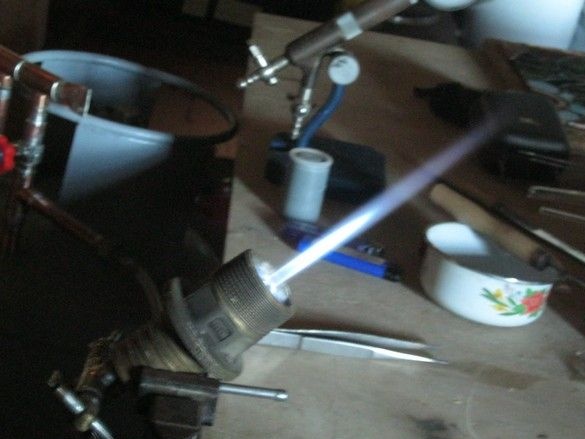
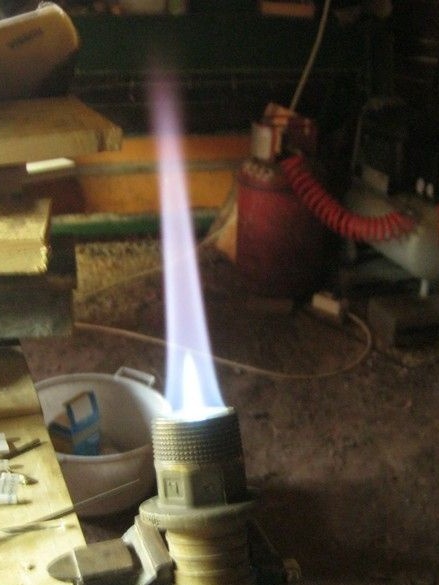
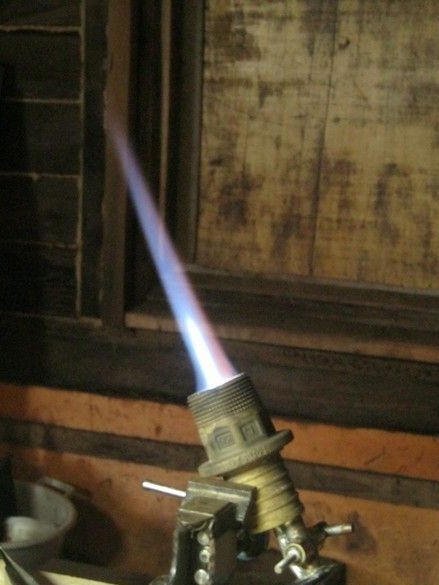
„Noga” do eksperymentalnego palnika nie została wykonana; podczas pracy zaciskała skrzynkę w małym imadle stołowym.
Powstała pochodnia jest znacznie większa niż pierwszy mały palnik, nawet z dodatkiem siostry gazowej. Szkło nagrzewa się znacznie szybciej, a większy obszar „przepływa”, można było napompować rurkę 18 mm z topliwego szkła „neonowego”. Okazuje się, że operacje, które wcześniej się nie powiodły - obrócenie krawędzi, przebicie grubą warstwą szkła igłą wolframową.Jednocześnie odczuwa się potrzebę dalszego wzrostu temperatury palnika. Nie ma wielu opcji - dodanie tlenu lub gazu wybuchowego.
Pracuj nad błędami. Sposoby dalszej poprawy.
Niemniej jednak tego rodzaju prace powinny być wykonywane przy użyciu metalowej tokarki, części i cała konstrukcja będzie dokładniejsza i dokładniejsza, dzięki czemu będą mniej bolesne. Średnica obudowy i dyszy jest oczywiście zbyt duża, wydaje się, że to nie pozwala uzyskać dłuższej pochodni miękkiego płomienia - prędkość gazu przy wpadaniu do szerokiej obudowy (dyszy) znacznie spada. Warto zbliżyć się do wielkości palnika w [1]. Byłoby fajnie zrobić dyszę, korpus, siatkę i przeponę z mosiężnego półfabrykatu, a nie z niczego - projekt można uczynić wygodniejszym w montażu i regulacji. Byłoby miło wykonać dyszę zgodnie z kartą - rzeźbiony, stożkowy polerowany otwór (patrz wyżej lub [1]). O tlenie lub „grzechotniku”, jak już powiedziano.
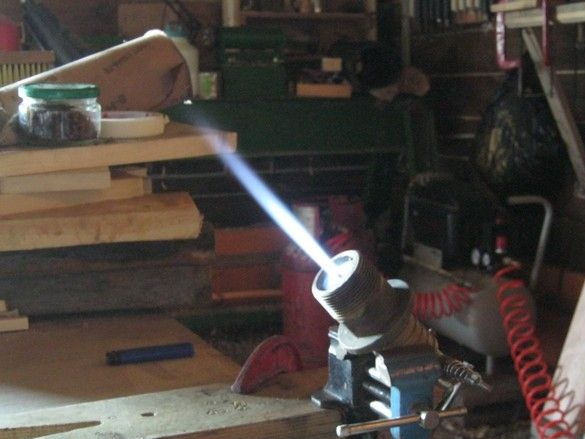
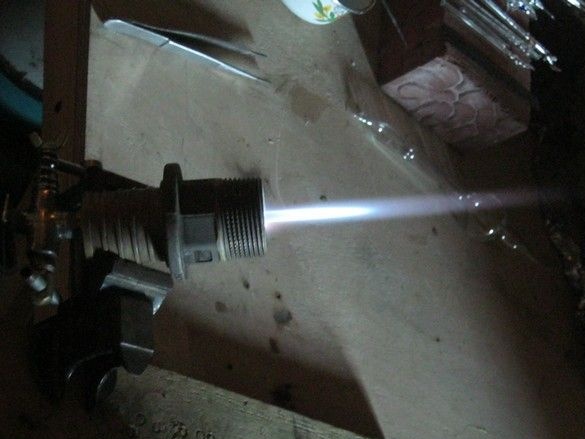

Literatura
1. Bondarenko Yu.N. Technologia laboratoryjna. Produkcja gazowo-wyładowczych źródeł światła
do celów laboratoryjnych i wiele więcej.