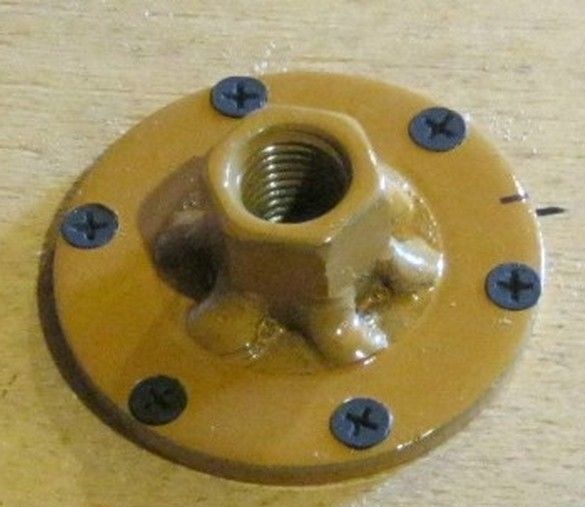
Po zbudowaniu tokarka do drewna, dobrze się bawił, skręcając w centrach. Po pewnym czasie stało się konieczne przetwarzanie bardziej różnorodnych przedmiotów. Musiałem poruszyć mózgiem, jakby z improwizowanych środków, bez dostępu do tokarki innej firmy (do metalu), zrobić odpowiedni sprzęt. Jeden z projektów okazał się bardzo tani, wygodny i pożądany.
Mocowanie zatrzaskowe często składało się z dwóch części - uniwersalnej małej metalowej płyty czołowej i specjalistycznej części drewnianej. Metalowa płyta czołowa może być również używana, jak zwykle, poprzez przykręcenie śrub do przedmiotu obrabianego.
Co zostało wykorzystane.
Narzędzia
Sama tokarka do drewna, noże do niej, zestaw narzędzi stołowych. Nie można tego zrobić bez maszyny do cięcia (szlifierki), lepiej jest użyć małej - jest wygodniejsza i bezpieczniejsza. Słuchawki do strzelania, gogle lub daszek. Nie wychodź też bez spawania odpowiednio - małego falownika i akcesoriów. Elektrody 2,5 mm. Często używany topliwy. Konieczne jest, aby ani wiertarka nie była wygodniejsza i dokładniejsza, jasne jest, że maszyna.
Materiały
Właściwie tylko odpowiednia liczba nakrętek i podkładek. Lepiej pomalować gotowy kawałek metalu, a następnie plus lakier. Małe drzewo dla „wąskiej specjalizacji”, często używam suchego drewna brzozowego o równych warstwach.
Więc Wrzeciono mojej tokarki kończy się gwintem M16, co pozwala na użycie standardowego sprzętu. W tym przypadku jest to „nakrętka przedłużająca”. Tnie się go na pół bezpośrednio na maszynie, włącza, obraca. Szlifierka kątowa. Należy go ostrożnie przyciąć. Na początku, na wyłączonej maszynie i bezczynnym młynie w rękach, ostrożnie przymierzaj, aby było wygodnie, gdziekolwiek są twoje łokcie i aby nie pasowały do niczego, co się obraca.
Maszyna włącza się i po przyjęciu wstępnie przetestowanej pozycji, włączonej przez młynek, uderzamy w znacznik na środku obracającej się nakrętki. Na początku szczególnie ostrożnie, dopóki krawędzie nie zostaną przycięte, potem zacznie ciąć bardziej równomiernie, a nacisk można nieznacznie zwiększyć.
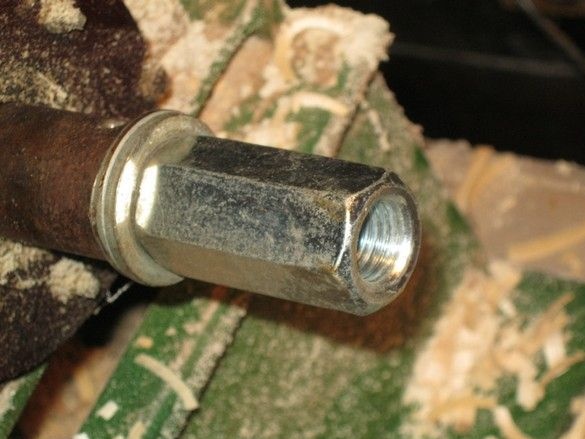
Po pewnym czasie naszych wysiłków ściana orzecha zostaje przecięta, a połowa spada.Wysokość każdej połowy, biorąc pod uwagę szerokość cięcia, okazuje się nieco większa niż w przypadku standardowej siostry, która nie jest „przedłużana”. Długość gwintu na wrzecionie mojej maszyny nie pozwala na użycie zwykłej nakrętki - wystaje spod gotowej płyty czołowej i powoduje wiele niedogodności później, podczas pracy.
Następnym krokiem będzie spawanie. Ze standardowego zakresu sprzętu wybieram „wzmocnioną podkładkę”, w niektórych sklepach nazywa się ją „podkładką do ciała” o odpowiedniej średnicy. Zwykle jest to prawie największy z dostępnego asortymentu. Musisz sprawdzić, czy nakrętka wpada w nią. Nakrętka powinna stać pośrodku otworu w podkładce. Ścięta nakrętka wytrzyma lepiej - po jednej jej stronie nie będzie fazowania, co należy wziąć pod uwagę, próbując nowego w sklepie.
Odcięta połowa jest przyspawana do podkładki. Zgrabnie Dobrze jest najpierw dokręcić je zaciskiem, ale zwykle okazuje się całkiem nieźle. Żebra są spawane w następującej kolejności - dowolna, a następnie odwrotnie. Obrabiany przedmiot obraca się o 90 stopni, ponownie dowolny z dwóch, a następnie odwrotnie. Jest więc mniejsze prawdopodobieństwo, że nakrętka ześlizgnie się z podkładki. Właściwie w pierwszych egzemplarzach próbowałem zorganizować „rowek” z tym samym młynem na obracającej się połowie nakrętki, aby zapewnić pewne dopasowanie w otworze, ale szlifierka kątowa nie jest narzędziem, które może dobrze wykonywać tę pracę - często z powodu niezbyt równej krawędzi „rowka” , nakrętka nie była bardzo wyrównana z podkładką.
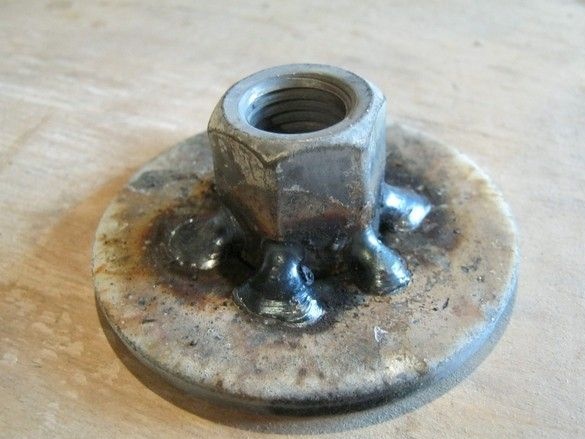
Po schłodzeniu przedmiotu obrabianego, jak zwykle, zamykamy szklaną skorupę żużla i kładziemy przedmiot na wrzecionie maszyny, podczas obrotu oceniamy bicie, jeśli są w rozsądnych granicach, korygujemy dołączoną szlifierkę kątową.

Jest to możliwe ze względu na estetykę i na odwrotnej stronie. Tutaj, ostrząc ołówkiem w odpowiednim miejscu obracającego się przedmiotu, zauważamy średnicę, wzdłuż której wiercone będą otwory. Aby użyć przyszłego panelu czołowego ze stosunkowo dużymi obiektami, można je wiercić więcej, do sześciu, jeśli w przypadku drobiazgów - trzy, cztery.
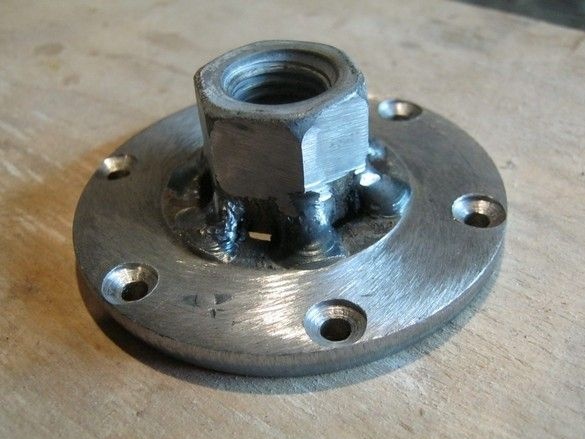
Później miło byłoby malować, dopóki nie pojawi się rdza - warstwa cynku jest częściowo spalona, częściowo odsączona. Poniżej wyskoczyła „ochra” ze sprayu, w dwóch warstwach, chociaż zwykle jestem leniwa.
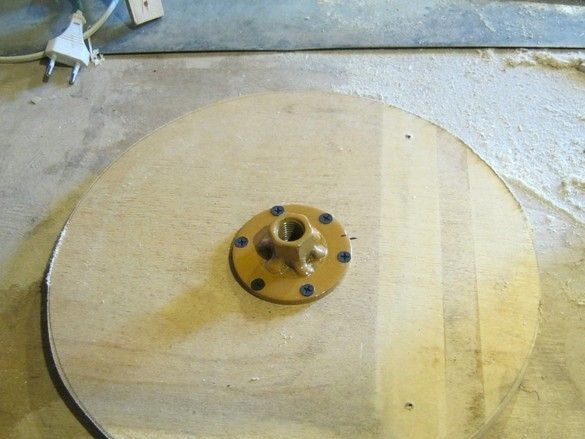
Na zdjęciu gotowa płyta czołowa na tarczy szlifierskiej wykonana jest z grubej sklejki. Na opresyjnym dysku klej PVA jest przyklejany, średniej wielkości, papier ścierny na bazie szmaty. Przez warstwę gazety, abyś mógł oderwać polizany pot.
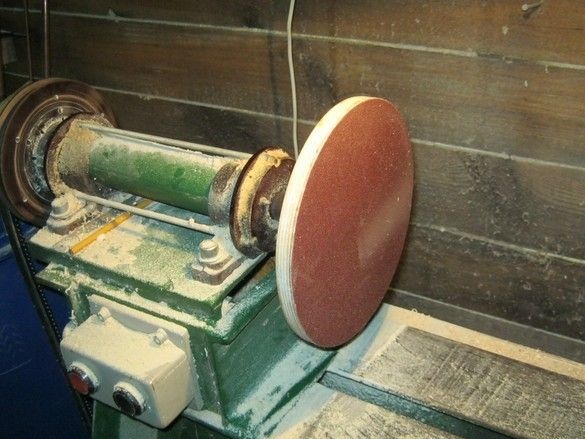
Do ostrzenia narzędzia, do przyklejania małych kawałków drewna.
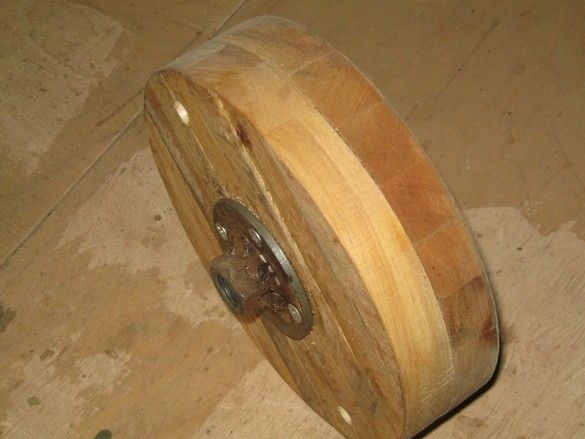
Podobny sprzęt, ale o mniejszej średnicy i przyklejony z bloków brzozy w dwóch warstwach z zakładką. Do ostrzenia narzędzi tokarskich. Na końcu znajduje się ten sam papier ścierny, na obwodzie zostanie przyklejony skórzany pasek w celu dokładnego dostrojenia pastą GOI.
I wreszcie wykorzystanie naszego panelu czołowego do bieżącej pracy. Podobnie jak zwykle, nasz mały jest wygodny w użyciu tam, gdzie trzeba zamontować obrabiany przedmiot na jednej krawędzi, bez tylnego środka. Jednocześnie bardzo wygodnie jest przykleić obrabiany przedmiot do bloku pośredniego. Kawałek deski nie jest przymocowany długimi śrubami i jest obrócony do dogodnej średnicy, przedmiot jest już do niego przyklejony. Klej topliwy.
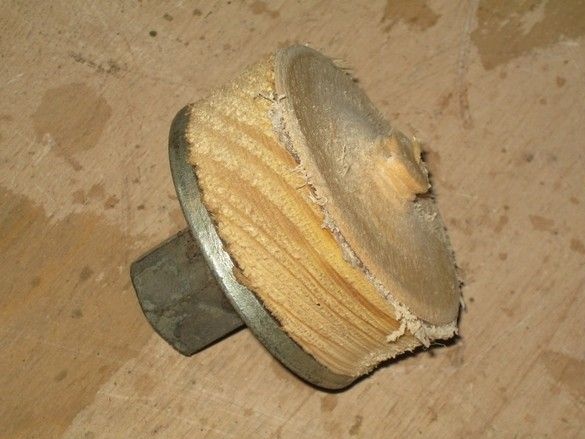
Na zdjęciu jest taki „nabój”, z resztą pozostawioną z obrabianego przedmiotu. Przed przyklejeniem następnego panel czołowy jest wkładany do maszyny i „odcinany” za pomocą narzędzia tnącego, odcinając resztki klejonego. Jednocześnie konieczne jest uchwycenie części starej warstwy kleju, aby (klej) nie gromadził się zbyt wiele.
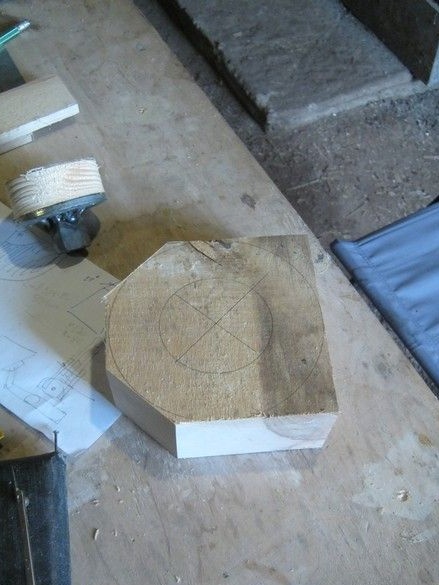
Przedmiot jest oznaczony, podczas gdy między innymi kompas, okrąg o średnicy jest rysowany nieco większy niż „blok” na płycie czołowej. Pozwala to dokładnie zorientować go po sklejeniu.
Smaruję obie powierzchnie do klejenia gorącym klejem, niekoniecznie całkowicie, wystarczy obwód na obwodzie, centymetry cofają się od krawędzi.
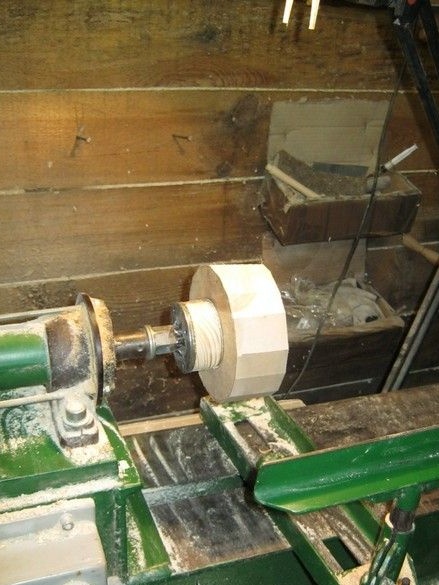
Początkowo przed całkowitym „oszukaniem” lepiej jest nacisnąć środek obrabianego przedmiotu z powrotem na środku, a następnie, gdy nie ma obciążeń udarowych, jest on usuwany.
Piękno takiej instalacji polega na bloku, w znacznie bardziej ekonomicznym zużyciu materiału obrabianego przedmiotu, ponadto podczas toczenia nie trzeba stale pamiętać, jak długo są śruby, aby nie wspiąć się na frez na głębokość.
Na deser - istnieje kilka opcji dla bardziej specjalistycznego oprzyrządowania opartego na wyprodukowanym panelu czołowym.
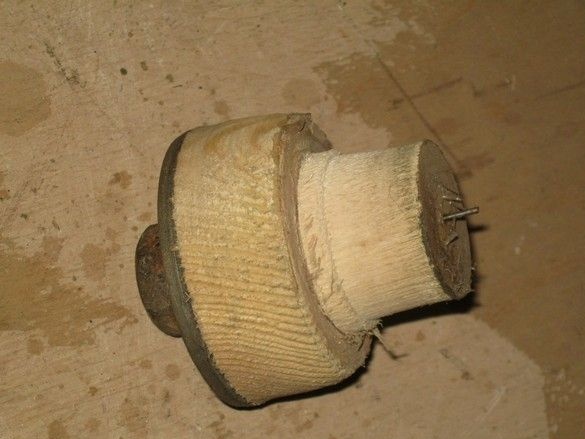
Na przykład w tym przypadku wymagane było, aby coś obracało się bardzo dokładnie wokół istniejącego centrum - tak łatwe jak łuskanie gruszek.
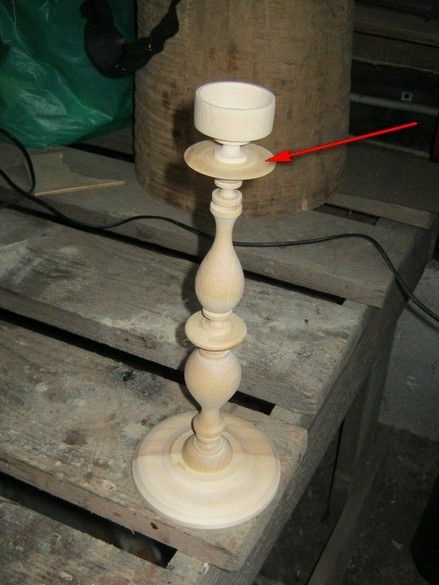
Lub na przykład - część świecznika wykonanego ze sklejki o grubości 6 mm lub cienkiej płyty brzozowej. Dla jego zaciśnięcia i obróbki dokonano takiego zatrzasku.
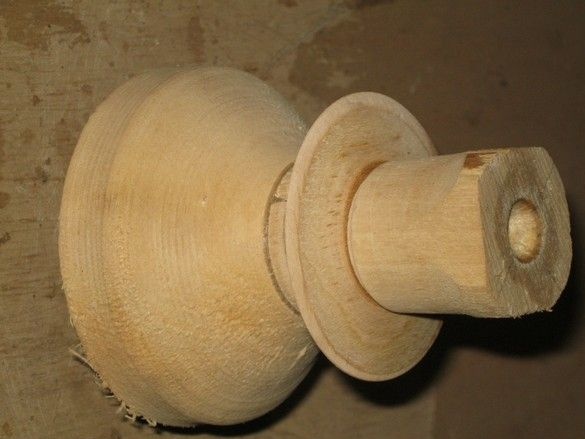
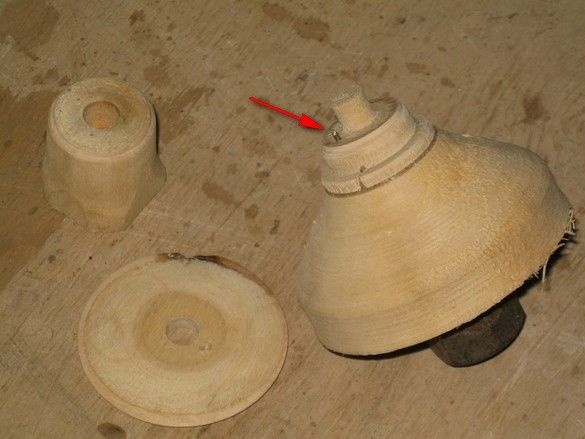
Ostre goździki zapobiegają obracaniu się przedmiotu. Zmontowane, dokręcone przez tylny środek.
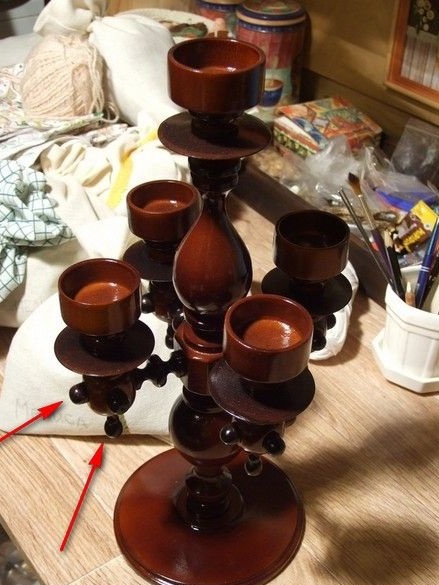
Przy produkcji kandelabrów potrzebna była pewna liczba drobnych części, takich jak pępki, musiałem wykonać prosty drewniany zacisk.
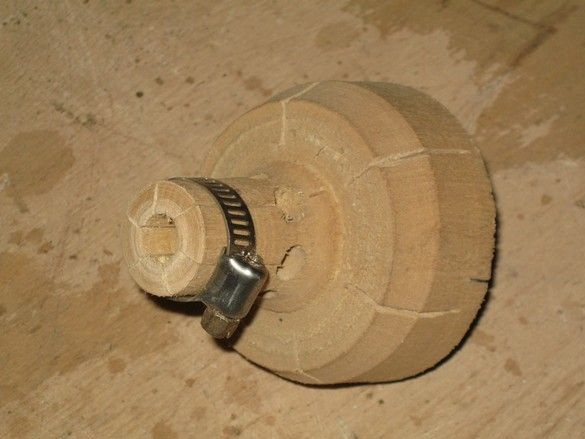
Pomimo nieco ograniczonych możliwości, ma również wiele zalet, a mianowicie łatwość produkcji, niski koszt. Podczas obróbki miniaturowych części, w pobliżu najbardziej „szczęk”, nie należy obawiać się zaczepienia „kartridża” za pomocą narzędzia, które w przypadku użycia analogu fabrycznego metalu czasami ma fatalne konsekwencje. Tak, bezpieczeństwo to znów wystające części, można je jeszcze bardziej zmniejszyć, jeśli zastąpisz metalowy zacisk ślimakowy wyżarzonym drutem stalowym lub miedzianym, a nawet zrobisz mały stożek na zewnętrznej stronie szczęk i wypełnisz pierścień do zaciskania. Metal lub drewno.
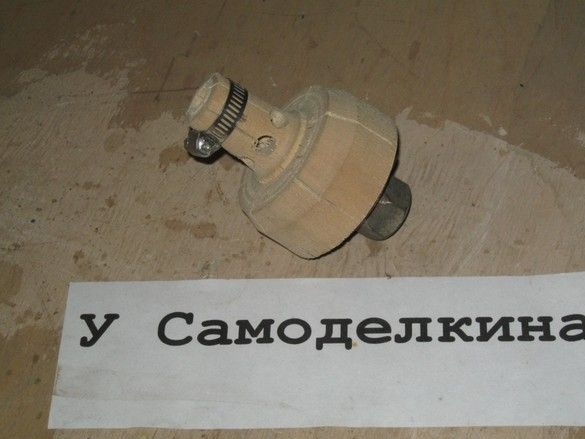
Przy produkcji uchwytu zaciskowego cylinder jest najpierw obracany, wiercony jest otwór środkowy (wiertarka), otwory są zaznaczane i wiercone z boku. Następnie w tokarce obrabiany jest przyszły zacisk - powstają niegrube szczęki. Na koniec wykonał cięcia płatków tulei zaciskowej.